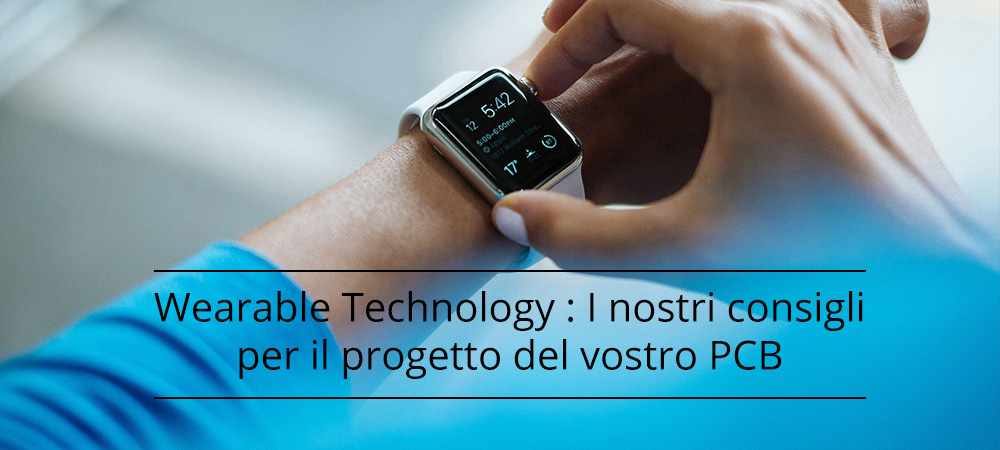
Negli ultimi anni, i dispositivi indossabili sono diventati sempre più popolari, grazie all’enorme progresso compiuto nel campo dell’elettronica e alla disponibilità di componenti elettronici integrati che hanno permesso di realizzare prodotti performanti, efficaci e di piccole dimensioni. Al centro di ogni dispositivo elettronico indossabile, sia esso uno smartwatch oppure un dispositivo elettromedicale (EMD), c’è un circuito stampato. Lo sviluppo di questi PCB rappresenta una sfida molto ardua per i progettisti. La dimensione e il peso ridotto, il basso assorbimento di potenza, l’affidabilità e la ridotta produzione di calore, non sono che alcuni dei criteri da soddisfare per creare un prodotto indossabile soddisfacente. A causa delle loro dimensioni estremamente ridotte e compatta e alla loro relativamente recente introduzione sul mercato, non esistono ad oggi dei criteri standard applicabili allo sviluppo di questo tipo di dispositivi. Ciononostante, è possibile applicare le stesse tecniche e raccomandazioni valide per circuiti con caratteristiche simili, facendo tesoro dell’esperienza acquisita durante lo sviluppo e la produzione di PCB ad elevata tecnologia.
Vincoli meccanici
La differenza più evidente fra un dispositivo elettronico standard e un dispositivo indossabile è sicuramente la dimensione. I dispositivi indossabili devono essere piccoli e leggeri, ma devono anche garantire la stessa affidabilità e funzionalità degli apparecchi di dimensioni maggiori. Ridurre al minimo dimensione e peso, utilizzando nello stesso tempo una forma geometricamente adeguata, non è un compito facile. Infatti, per questo genere di dispositivi è necessario ottimizzare la posizione dei componenti e delle piste sul PCB, avendo a disposizione uno spazio ridottissimo. Il routing automatico non è consigliato in questi casi ed è dunque preferibile effettuare un routing manuale. Il PCB deve potersi adattare alla forma del contenitore. Infatti, è assai raro che un circuito destinato a questo tipo di dispositivi abbia una forma rettangolare e rigida, mentre è più frequente trovare dei circuiti multistratato sottili e con contorni curvilinei, in grado di entrare nel contenitore del prodotto finito. La scelta dei componenti gioca comunque un ruolo fondamentale e si tende a privilegiare componenti con footprint ridotto e package a basso profilo per minimizzare lo spessore del prodotto.
Strettamente legato ai vincoli meccanici, un altro aspetto che non deve essere trascurato dai progettisti riguarda sicuramente l’umidità, potenzialmente in grado di danneggiare o alterare il funzionameneto dei circuiti elettronici, soprattutto se ad alta impedenza. Il dispositivo indossabile, essendo per la maggior parte del tempo a contatto con il corpo umano che tende a produrre liquidi e umidità, deve essere fornito di un PCB progettato e costruito per sopportare l’umidità. A seconda dei casi, i progettisti possono decidere di seguire due soluzioni differenti oppure, in alcuni casi, adottarle entrambe. La soluzione meccanica prevede l’utilizzo di un contenitore realizzato con materiali appositi e impermeabili, chiuso ermeticamente per impedire all’umidità di penetrare. L’altra opzione è quella di realizzare sul circuito interno una tropicalizzazione tramite conformal coating, impedendo così all’umidita di danneggiare la parte elettronica. Entrambe le soluzioni sono possibili.
Un altro aspetto da non sottovalutare dei dispositivi indossabili riguarda le perdite di corrente elettrica, tenendo presente che spesso la corrente di funzionamento è solo di qualche nano ampere. È importante sottolineare come componenti non correttamente isolati possano creare una dispersione elettrica in zone differenti del dispositivo, una situazione da evitare quando il dispositivo può entrare in contatto con la pelle dell’utilizzatore. Un cattivo isolamento dei componenti può folgorare l’utente in modo più o meno grave, oltre a provocare il surriscaldamento e la scarica rapida della batteria.
e riceverete un preventivo per il vostro progetto di PCBA entro 10 minuti!
Selezione dei materiali
Gli strati del PCB, tra loro isolati tramite pre-preg, possono essere composti da strati di FR4, Poliyamide o Rogers. Dal momento che i dispositivi indossabili devono essere affidabili e devono essere spesso in grado di gestire segnali di elevata velocità e frequenza, a livello tecnico vengono utilizzati dei materiali più all’avanguardia rispetto all’FR4, il materiale più comunemente utilizzato per il suo basso costo e la facile reperibilità. Il materiale FR4 ha una costante dielettrica (DK) pari a 4,5, mentre materiali più avanzati come il Rogers 4003 e il Rogers 4350 hanno rispettivamente un DK pari a 3,55 e 3,66. Quando si devono gestire segnali di elevata frequenza, è necessario limitare le perdite di potenza e pertanto un materiale come il Rogers 4350 è preferibile. Inoltre, l’FR4 ha un fattore di dissipazione (DF) più elevato dei materiali Rogers, in particolare nel funzionamento alle alte frequenze.
Ciò significa che utilizzando il laminato FR4 con segnali ad alta frequenza si creano delle insertion loss significative, riducendo la potenza e la capacità di trasmissione dei segnali elettrici. Sebbene la riduzione dei costi di produzione sia un fattore importante nello sviluppo di questo prodotto, occorre notare come un PCB realizzato con laminati Rogers offra prestazioni e affidabilità superiori a quelle del tradizionale FR4, il tutto a un costo complessivo accettabile. Per le applicazioni nel settore consumer, dove la concorrenza è spietata, si può comunque utilizzare una soluzione ibrida per PCB, ottenuta combinando l'FR4 a base epossidica con il Rogers e altri strati di materiale standard FR4. Inoltre, i materiali Rogers come quelli della serie 4000 presentano un coefficiente di dilatazione termica (CTE) particolarmente stabile. Ciò significa che quando il PCB subisce un ciclo termico con raffreddamento e surriscaldamento, l'espansione e la contrazione subita dal circuito stampato vengono mantenute entro un limite ristretto e limitato, soprattutto rispetto a quanto avviene per il materiale standard FR4. Questa stabilità si mantiene anche a seguito di un aumento della frequenza e della temperatura.
Per quanto riguarda la struttura del PCB, i dispositivi indossabili utilizzano tipicamente un circuito composto da quattro a otto strati, inserendo tra i vari layer un numero opportuno di piani di massa e di potenza. In questo modo, i fenomeni di crosstalk che possono verificarsi tra piste adiacenti sono ridotti al minimo, migliorando la compatibilità elettromagnetica grazie a una riduzione degli effetti prodotti dalle interferenze elettromagnetiche (EMI). Nella definizione del layout della scheda, il piano di massa deve essere posizionato vicino al piano di distribuzione della potenza. Ciò riduce virtualmente a zero il rumore, un aspetto molto importante soprattutto nelle applicazioni a radiofrequenza (RF).
Definizione del PCB
La realizzazione del circuito elettronico di un dispositivo indossabile non si limita al PCB, ma deve tener conto di altri materiali come tessuti, plastica e schede rigido flessibili. A differenza dei circuiti stampati rigidi tradizionali, i PCB flessibili e rigido flessibili hanno una maggiore durata e offrono una maggiore resistenza a calore, umidità, agenti atmosferici e vibrazioni. Queste soluzioni avanzate non hanno soltanto il vantaggio di essere flessibili, ma occupano anche meno spazio, sono più leggere e più resistenti. In Figura 1 è visibile un esempio di PCB rigido flessibile adatto ai dispositivi indossabili.
Figura 1: Esempio di PCB rigido flessibile.
Tuttavia, l'utilizzo di un PCB rigido flessibile non è così semplice, e per questo motivo è preferibile seguire alcune linee guida e precauzioni. Prima di tutto, occorre prestare particolare attenzione al perfetto allineamento tra gli elementi che compongono il circuito, tenendo presente che il PCB dovrà occupare uno spazio ben definito e limitato. Un altro aspetto particolarmente insidioso riguarda la progettazione dello stackup. Le parti flessibili e rigide del circuito devono essere integrate nel dispositivo, prevedendo la posizione finale che esse assumeranno all’interno del dispositivo. In questa fase delicata è possibile utilizzare un software appropriato, in grado di fornire un modello 3D del PCB o dell'intero dispositivo. Le tracce associate ai segnali ad alta frequenza non devono essere posizionate vicino ai piani di massa, ma devono essere posizionate tra i bus di alimentazione per attenuare il jitter generato dalla perturbazione del segnale. Particolare attenzione deve essere posta al controllo dell'impedenza, tenendo presente che alle alte frequenze una differenza anche piccola di impedenza può causare problemi alla trasmissione e ricezione del segnale, con conseguente distorsione.
Nella progettazione di un PCB per dispositivi indossabili sono largamente utilizzate le microstrip, le stripline e le guide d'onda complanari, poiché queste tecniche di connessione sono in grado di eliminare il rumore tipico dei sistemi RF. In generale, è consigliabile introdurre dei filtri di bypass, condensatori di disaccoppiamento e un numero sufficiente di piani di massa. Il filtro di bypass sopprime l'ondulazione prodotta dal rumore e riduce i fenomeni di crosstalk; il condensatore di disaccoppiamento deve essere posizionato vicino alle linee di alimentazione. In Figura 2 è mostrato il circuito stampato di uno smartwatch, il quale evidenzia un'elevata densità di componenti tra cui processore, transceiver RF, codec audio, modulo di gestione dell'alimentazione, processore in banda base e antenne wireless multiple.