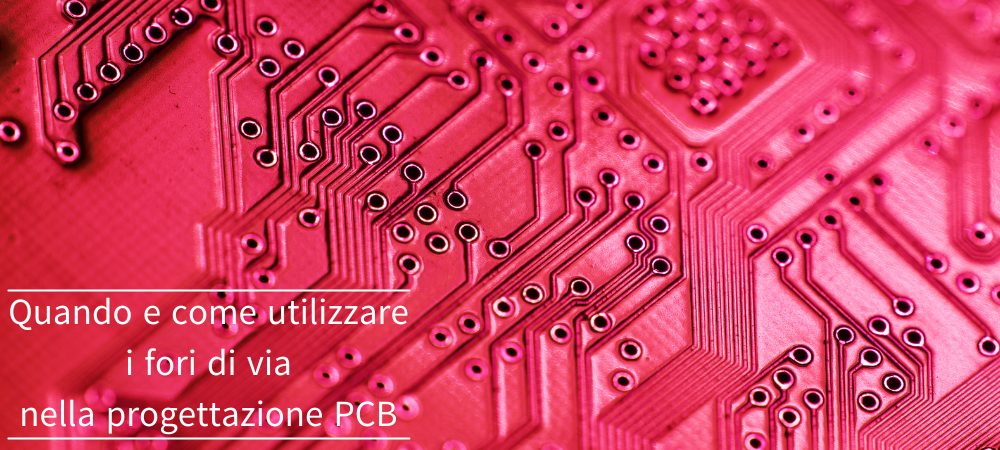
Con il termine via (o foro di via) si intende una connessione elettrica tra layer differenti di un circuito stampato. Il via è in pratica un piccolo foro praticato nei laminati del PCB che attraversa due o più layer adiacenti. Il foro viene ricoperto internamente di rame (tramite processo galvanico, rivettatura, o inserimento di un piccoloo tubo di materiale conduttivo), formando una connessione elettrica nel materiale isolante che separa i layer del PCB.
In base alle specifiche esigenze dell’applicazione, una scheda elettronica può richiedere fori di via che attraversano tutti i layer dello stackup, oppure soltanto uno dei due layer più esterni, oppure ancora soltanto due o più layer interni al PCB. Come vedremo più avanti nell’articolo, esiste anche una particolare categoria di via, noti come via termici, la cui funzione è quella di dissipare il calore prodotto dai componenti, anziché realizzare una connessione elettrica tra i layer del PCB.
e riceverete un preventivo per il vostro progetto di PCBA entro 10 minuti!
È inoltre importante sottolineare come i via non debbano essere confusi con i fori PTH (Plated Through Hole), i quali sono normalmente utilizzati per il collegamento elettrico, sul PCB, dei componenti a foro passante. I fori PTH, che hanno dimensioni superiori rispetto a quelle dei via, possono anche essere utilizzati per realizzare una connessione meccanica sulla scheda di alcuni componenti, come ad esempio i connettori. In Figura 1 è visibile una porzione di PCB con componenti a montaggio superficiale (SMD), in cui si nota la presenza di un elevato numero di via.
Figura 1: fori di via su un PCB
Tipi di via
I fori di via possono essere raggruppati in tre classi principali, in base alla loro posizione all’interno dello stackup e al numero di layer da essi attraversato:
- via passanti (through hole via): questi via attraversano tutti i layer del PCB, incluse le due facce esterne del circuito stampato. In genere hanno dimensioni maggiori rispetto agli altri tipi di via e sono più semplici da realizzare in quanto non occorre arrestare il processo di foratura nel punto desiderato;
- via sepolti (buried via): in questo caso, il via giace tutto internamente al circuito stampato ed è quindi privo di collegamenti verso i layer esterni. Nel caso di una scheda multistrato, la placcatura interna di un buried via deve necessariamente essere completata prima di applicare alla scheda i due layer più esterni. I via sepolti sono anche molto utili per ridurre l’aspect ratio del PCB, ovvero il rapporto tra lo spessore del PCB e il diametro del foro di via;
- via ciechi (blind via): questi fori di via partono da una delle facce esterne del PCB e attraversano uno o più layer interni, senza però congiungersi con la faccia opposta del PCB. Dal punto di vista delle fabbricazione, i via ciechi presentano alcune difficoltà, in quanto occorre determinare con precisione quando arrestare il processo di foratura della scheda in modo da ottenere il grado di profondità desiderato. I via ciechi sono molto utili per aumentare il numero di collegamenti tra un layer interno e l’esterno, con possibile riduzione del numero di tracce e quindi del costo finale del PCB.
Da quanto esposto risulta evidente come la presenza dei via passanti possa in teoria essere rilevata anche ad occhio nudo, in quanto essi possono essere attraversati dalla luce, mentre per i via sepolti e i via ciechi ciò non sia possibile. Le tre categorie di via sono rappresentate graficamente in Figura 2.
Figura 2: tipi di fori di via
L’evoluzione dei componenti elettronici verso una sempre maggiore densità di integrazione, con conseguente aumento del numero di pin di interconnessione, ha determinato la diffusione nell’ambito della progettazione di fori di via applicati direttamente sui pad BGA (Ball Grid Array), noti anche come via in pad. Per i produttori di circuiti stampati, i via in pad rappresentano un vantaggio, in quanto consentono di ridurre lo spazio sul PCB richiesto dai via tradizionali, ottenendo schede con dimensioni inferiori. I via in pad, tuttavia, possono presentare dei problemi durante la fabbricazione del PCB. In particolare, il processo di saldatura può causare il riempimento del foro, rendendolo inutilizzabile. Per questo motivo, è in genere consigliabile ridurre al minimo il numero di via in pad.
I microvia
Una classe di via a parte è rappresentata dai microvia, che a differenza dei tipi precedenti sono utilizzati esclusivamente sui circuiti stampati con elevato numero di interconnessioni (HDI). È prassi comune ritenere che si possa parlare di microvia quando il diametro del foro è pari o inferiore a 150 µm. In realtà, lo standard IPC ha rivisto nel 2013 la definizione di microvia, definendolo ora come un foro con aspect ratio (rapporto tra il diametro del foro e la sua profondità) pari a uno. Inoltre, la profondità di un microvia non deve mai eccedere il valore di 0,25 mm. Per ottenere fori di dimensione così piccola, è necessario utilizzare la microforatura laser, un processo in continua evoluzione, potenzialmente in grado di creare microvia con diametro anche inferiore a 15 µm. La microforatura laser, che inevitabilmente introduce dei costi addizionali, viene normalmente eseguita prima del processo di laminazione dei layer.
Come visibile in Figura 3, i microvia hanno una tipica forma a cono, un aspetto che semplifica notevolmente il processo di placcatura delle pareti interne. Ogni singolo microvia può attraversare al massimo due layer adiacenti. L’ampia diffusione dei dispositivi mobili, come smartphone e indosssabili, hanno determinato un’evoluzione dei microvia da strutture singole a strutture più complesse, composte da microvia multipli. Nel caso infatti il progetto del PCB richieda via che attraversano più layer, i microvia possono essere sovrapposti nella configurazione “stacked”. Una configurazione alternativa alla precedente è quella “staggered”, in cui i microvia praticati sui layer adiacenti sono sfalsati tra loro.
Figura 3: struttura e tipi di microvia
Rispetto ai fori di via normali, i microvia presentano il vantaggio di ridurre le dimensioni del PCB nelle schede con elevato numero di connessioni. Inoltre, i microvia sono particolarmente utili in alcune applicazioni, come il breakout delle BGA con passo di 0,65 µm. Nei circuiti audio, i microvia riducono i fenomeni di crosstalk e, nelle applicazioni ad alta velocità e ad alta frequenza, forniscono una migliore protezione dalle interferenze elettromagnetiche. L’effetto radiante, determinato dalla particolare struttura geometrica del via che può comportarsi come una vera e propria antenna, è infine molto inferiore nei microvia, rispetto ai via tradizionali.
I microvia non sono tuttavia esenti da problemi o difetti che possono compromettere l’affidabilità della scheda elettronica. Il principale problema è legato all’insorgenza di ICD (acronimo di InerConnect Defects) in prossimità della placcatura interna dei fori, che possono causare circuiti aperti e altri problemi intermittenti nel funzionamento alle elevate temperature.
Via termici
I componenti attivi, come i dispositivi elettronici di potenza (MOSFET, diodi e power module), i microprocessori ad elevate prestazioni e i componenti ad alta frequenza, sviluppano una quantità considerevole di calore che può essere meglio dissipata tramite l’adozione di via termici.
La maggior parte dei circuiti stampati è basata sull’FR-4, un materiale relativamente economico che però presenta un'elevata resistenza termica. Ne consegue che il calore si accumula vicino al fondo del componente, comportando un elevato aumento della temperatura e la potenziale formazione di hot spot. I via termici, posti a diretto contatto dei componenti attivi, favoriscono un migliore trasferimento del calore, consentendo al componente di funzionare a temperature di esercizio inferiori, il più possibile vicine alla temperatura ambiente. Affinché siano efficaci, i via termici devono essere collocati il più possibile vicini (meglio se al di sotto) del componente che sviluppa calore. Poiché ogni via termico presenta una conduttività termica maggiore rispetto al substrato di FR-4, posizionando più via termici si riduce la resistenza termica della struttura e si riesce a trasferire una quantità maggiore di calore. I via termici hanno anche una certa induttanza, per cui è preferibile collocare più via in parallelo, collegandoli al piano di massa per fornire un percorso di ritorno con induttanza inferiore.
Per quanto riguarda la struttura fisica, i via termici sono in genere del tipo a foro passante, rivestiti internamente di resina epossidica conduttiva e sottoposti a successiva placcatura. Il via termico si comporta pertanto come un tubo in grado di trasferire il calore da un componente posto su uno dei layer superficiali verso i layer più interni. I via termici sono inoltre ricoperti con una solder mask sul lato posteriore della scheda per evitare che la saldatura attraversi i fori.
La determinazione del numero, dimensione e posizionamento dei via termici è oggi facilitato dalla disponibilità di strumenti software in grado di eseguire un’analisi termica del circuito nelle varie condizioni operative e con diversi valori della temperatura ambiente.
18/11/2021