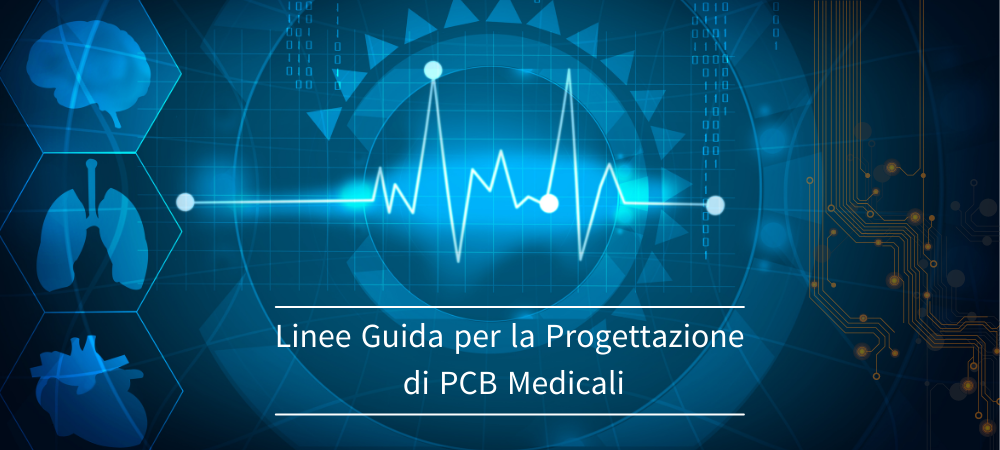
I circuiti stampati hanno assunto una rilevanza critica per le applicazioni elettromedicali. I significativi progressi compiuti nel campo delle tecnologie elettroniche hanno infatti permesso la realizzazione di dispositivi medicali con funzionalità sempre più avanzate, come pacemaker, defibrillatori, monitor cardiaci per la cura di patologie cardiovascolari, diagnostica per immagini, risonanza magnetica, TAC, apparecchiature a ultrasuoni, oltre a un’ampia gamma di soluzioni portatili o indossabili, come termometri, monitor della glicemia e apparecchiature per la stimolazione muscolare elettrica.
Per stare al passo con queste innovazioni, i progettisti devono garantire che i PCB di grado medico siano conformi agli standard di sicurezza applicabili, siano sicuri sia per il paziente, sia per gli operatori sanitari, abbiano un’elevata affidabilità e durata nel tempo.
e riceverete un preventivo per il vostro progetto di PCBA entro 10 minuti!
Tecnologie per i PCB medicali
Come già avvenuto in altri settori dell’elettronica, anche per i dispositivi elettromedicali la tendenza attuale è quella di sviluppare prodotti sempre più piccoli e con densità sempre maggiore di componenti. Ciò, ovviamente, comporta diverse conseguenze sulla progettazione del circuito stampato, come ad esempio la disposizione dei componenti e le relative distanze, la lunghezza e la distanza tra le tracce, la dissipazione termica del PCB. Ne consegue che i margini di errore nella progettazione di una scheda sono diminuiti drasticamente, richiedendo spesso una maggiore flessibilità sia durante la progettazione, sia nella fase di produzione.
Una tecnologia PCB in grado di rispondere a questa esigenza è quella che consente di realizzare schede ad alta densità di connessioni (HDI). Riducendo le dimensioni del PCB e aumentando il numero e la complessità delle funzionalità implementate, si riduce l’area disponibili per il routing delle tracce, le quali sono sempre più vicine tra loro.
Un’altra tecnologia largamente impiegata nei PCB medicali è quella dei circuiti stampati flessibili e rigido flessibili. Ciò avviene perché i dispositivi medicali spesso non sono conformi agli standard tipici di forma e dimensione dei PCB tradizionali e devono essere in grado di adattarsi a un'area più piccola possibile, garantendo gli stessi standard di affidabilità e resistenza. I PCB flessibili sono realizzati con materiali più leggeri, riducendo il peso complessivo del dispositivo. La capacità di questi PCB di flettersi consente di ottimizzare gli spazi disponibili e i costi di produzione, lasciando al progettista maggiore libertà nello scegliere la forma del contenitore. Sebbene la progettazione di un PCB flessibile sia più complessa rispetto a quella di un PCB rigido, diventa molto più facile sviluppare un dispositivo ergonomico e robusto. I PCB flessibili offrono infatti significativi vantaggi meccanici rispetto ai PCB rigidi in numerose applicazioni medicali, soprattutto quelle indossabili. Inoltre, i PCB flessibili possono essere interfacciati con schede rigide attraverso sottili cavi piatti, senza richiedere connettori alti e ingombranti.
La tendenza attuale di molti dispositivi indossabili, come l'automonitoraggio dei parametri vitali per l'esercizio fisico, il benessere o le condizioni cliniche, sta favorendo lo sviluppo di dispositivi con fattori di forma del PCB non standard, come rotonda o ellittica. Altre volte, il PCB può assumere forme completamente irregolari. L'integrazione di PCB flessibili e rigido-flessibili, compatti e ad elevata densità, consente ai progettisti di gestire facilmente le forme più disparate di circuito stampato. In Figura 1 è visibile un esempio di PCB rigido flessibile.
Figura 1: un PCB rigido flessibile
Nei prossimi paragrafi verranno presentate alcune semplici regole che possono aiutare il progettista nello sviluppo di PCB medicali, semplificandone la progettazione, il test e la manutenzione.
1 – Componenti SMD o PTH
Anche se la tecnologia di montaggio superficiale (SMT) si è oramai imposta nella maggioranza delle applicazioni elettroniche, per alcuni dispositivi può ancora avere senso utilizzare la tecnica con montaggio a foro passante (PTH), soprattutto sulle schede di alimentazione o dove sono presenti diversi connettori.
In generale, nelle applicazioni medicali è preferibile utilizzare la tecnologia SMT, in quanto consente di utilizzare componenti di dimensioni ridotte, riducendo la dimensione del PCB e aumentando la densità dei componenti sulla scheda. Inoltre, per il montaggio di componenti SMD non è necessario praticare alcun foro, riducendo sia i costi, sia il tempo richiesto per la fabbricazione e assemblaggio del circuito stampato.
Uno tra i più piccoli package SMD attualmente disponibili in commercio è lo 008004, visibile in Figura 2, con dimensioni di soli 0,25mm x 0,125mm.
Figura 2: alcuni tra i più piccoli package SMD
2 – Materiali
Data la particolare criticità dei dispositivi medicali, dal cui funzionamento sicuro e affidabile dipende spesso la vita di molti pazienti, la scelta dei materiali utilizzati per la fabbricazione del PCB è particolarmente critica. I principali fattori che guidano la scelta dei materiali e substrati più adatti a una specifica applicazione medicale sono i seguenti:
- conformità alla normativa RoHS;
- presenza di segnali RF e/o segnali ad elevata frequenza/velocità di trasmissione;
- massima temperatura di esercizio;
- opzioni per la connettività;
- dimensioni e forma dell’involucro.
Per supportare l’elevata densità di componenti richiesta, è frequente l’utilizzo della tecnologia HDI, con conseguente elevato numero di interconnessioni e fori di via sia ciechi, sia interrati. La tecnologia HDI consente di ridurre drasticamente le dimensioni del PCB, grazie anche alla possibilità di realizzare fori di via perforati al laser, via-in-pad e tracce con larghezza e spaziatura di soli 5 mil.
La tecnologia via-in-pad, utilizzata soprattutto con componenti ad elevata integrazione, come le BGA, o dotati di un elevato numero di pin e passo molto stretto, consente di creare direttamente sui pad i fori per la connessione delle piazzole agli strati interni. In Figura 3 è visibile un esempio di applicazione della tecnologia via-in-pad, con fori di via praticati direttamente su alcuni pad del componente.
Figura 3: via-in-pad
Occorre tuttavia sottolineare come la produzione di PCB HDI per uso medicale richieda investimenti in apparecchiature costose, come l'imaging diretto laser (LDI) e i processi additivi e semi-additivi (mSAP), le quali comportano un maggiore costo di produzione del PCB. Tali apparecchiature si rendono necessarie per soddisfare i requisiti stringenti relativi alla larghezza delle tracce e alla loro spaziatura.
Per quanto riguarda il materiale per i laminati, l’FR-4 (Flame Retardant Level 4) rappresenta una scelta comune anche per i PCB medicali, in virtù del suo basso costo e della sua fabbricazione relativamente semplice. Nel caso di apparecchiature più sofisticate, oppure appartenenti a classi di rischio superiori, il PCB può richiedere dei laminati speciali come poliammide, teflon, PTFE o materiali di tipo ceramico. Questi materiali sono particolarmente adatti a tutte le applicazioni elettroniche ad elevata frequenza. La costante dielettrica del materiale FR-4 (indicativamente pari a circa 4,5) si dimostra in questi casi troppo elevata, comportando significative perdite di segnale durante la trasmissione attraverso il circuito stampato. Viceversa, materiali come il teflon offrono valori di costante dielettrica pari a 3,5 o inferiore. Oltre ad una riduzione della costante dielettrica, questi materiali offrono anche caratteristiche termiche eccezionali, raggiungendo valori di Tg fino a 280°C.
3 – Longevità
Nella fase di progettazione di un PCB medicale è fondamentale che i progettisti, collaborando con i fornitori dei componenti e i produttori del circuito stampato, siano in grado di prevedere l'obsolescenza dei componenti utilizzati. Ciò che si vuole evitare è la prematura fine vita del progetto causata dall’impossibilità di reperire determinati componenti. Se ciò avviene e la modifica richiesta a livello di componente o schema elettrico è sufficientemente significativa, il prodotto potrebbe dover ripetere da capo il processo di approvazione al fine di ottenere le conformità richieste (l'approvazione da parte degli enti preposti può richiedere diversi mesi).
4 – Manutenibilità
Ogni fase del progetto del PCB deve porsi come obiettivo la facilità di assemblaggio e manutenzione. Ciò, ovviamente, influisce su vari aspetti, come posizionamento dei componenti, layout del PCB e routing delle tracce.
Particolare attenzione deve essere posta ai connettori, in modo tale che siano facilmente raggiungibili dagli installatori o manutentori senza provocare impedimenti. Tutte le piazzole devono avere posizione e dimensioni tali da semplificare l’operazione di saldatura, come pure l’orientamento dei componenti dotati di elevato numero di pin. Occorre cercare di mantenere un PCB con profilo in altezza il più possibile uniforme, separando dagli altri i componenti con altezza maggiore.
Infine, si consiglia di realizzare un modello 3D dell’intero circuito, un’operazione che oggi può essere eseguita in modo quasi automatico da molti strumenti di sviluppo per PCB. Il modello consente di valutare le dimensioni e gli ingombri effettivi della scheda, fornendo importanti suggerimenti per la fase di assemblaggio e installazione all’interno del contenitore.
5 – Test e debug
L’intera scheda deve essere progettata in modo tale da semplificare sia il test, sia il debug del circuito. Prevedere inoltre un numero sufficiente di test point per facilitare la fase di diagnostica, sia in fabbrica, sia sul campo. I test point andrebbero collocati soprattutto sulle tracce che trasportano il segnale, sui segnali di clock e controllo e sulle linee di alimentazione. L’esperienza dimostra come sia sempre meglio avere qualche test point in più, piuttosto che qualcuno mancante nei punti più critici del circuito. Inoltre, se possibile, è sempre meglio collocare i test point sulle facce esterne della scheda. Quando il circuito stampato è assemblato e installato nel contenitore, la fase di test e verifica sarà molto più semplice.
6 – Simulazione
Le tecniche di simulazione, come il Digital Twin, apportano dei benefici considerevoli nella progettazione dei PCB medicali, riducendo sia i costi di sviluppo, sia il time to market. Il principale vantaggio della simulazione è quello di individuare potenziali errori prima ancora di realizzare il primo prototipo di scheda. La tecnologia Digital Twin crea in sostanza un modello virtuale del circuito, prendendo in ingresso i dati provenienti dal mondo reale e producendo in uscita una simulazione o una previsione di come il circuito si comporterà come effetto dell’applicazione di quegli ingressi. Ciò consente l'analisi dei dati e il monitoraggio del sistema, consentendo agli ingegneri di prevenire i problemi prima che si verifichino, determinare i tempi di fermo e ottimizzare le prestazioni del prodotto. Altrettanto importante è la simulazione termica del circuito, la quale consente di individuare precocemente la formazione di possibili hot-spot durante il funzionamento del circuito nelle diverse condizioni operative di utilizzo. È sempre meglio spendere qualche ora apportando qualche modifica al circuito elettrico e rieseguendo la simulazione termica, piuttosto che eseguire una costosa analisi termica con telecamere a infrarosso sul prodotto finale, accorgendosi che sono richieste modifiche al circuito per soddisfare i requisiti di affidabilità e sicurezza imposti dagli standard.