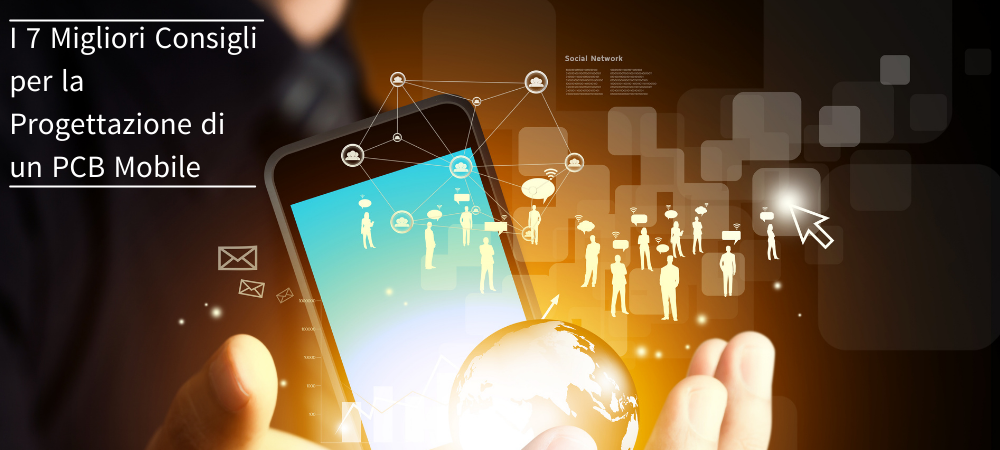
Il progressivo aumento delle funzionalità integrate nei dispositivi mobile di ultima generazione sta imponendo dei requisiti sempre più stringenti alla progettazione dei circuiti stampati. Connettività Wi-Fi e Bluetooth, supporto per le reti mobili 4G e 5G, integrazione con un un numero sempre maggiore di sensori rappresentano per i progettisti elettronici delle sfide tecnologiche senza precedenti. I dispositivi mobile, a partire dagli smartphone, si stanno evolvendo verso una maggiore intelligenza, miniaturizzazione e multifunzionalità, richiedendo dei circuiti stampati sempre più complessi in grado di supportare tali richieste (la tendenza imposta dal mercato è quella di avere dispositivi sempre più sottili, con spessori normalmente inferiori a un centimetro).
e riceverete un preventivo per il vostro progetto di PCBA entro 10 minuti!
Sfide progettuali
La tendenza di sviluppo degli attuali smartphone richiede necessariamente dei circuiti stampati multistrato (composti da 10 o più layer) per realizzare la scheda madre e uno o più PCB con numero ridotto di layer per le schede ausiliarie, eventualmente realizzate con PCB rigido flessibili. L’utilizzo sempre più esteso di componenti SiP (System-in-Package) e di SoC (System-on-Chip) multi core, disponibili anche con architettura a 64 bit, nonché la riduzione della spaziatura dei pin da 0,4mm a 0,35mm, sono probabilmente destinati a contrastare la crescita del numero di layer, se non addirittura portare a una loro riduzione.
I progettisti di PCB mobile devono prestare la massima attenzione agli aspetti tecnologici sin dalle prime fasi dello sviluppo. I principali fattori da considerare durante la progettazione del circuito stampato includono:
- definizione del layout, dei fori di posizionamento e dei fiducial marker richiesti per la produzione e l'assemblaggio automatici;
- definizione dei pannelli richiesti nella fase di produzione del PCB;
- selezione dei materiali utilizzati per i substrati, selezione dei componenti e del relativo package;
- posizionamento dei componenti e relativa spaziatura tra di essi.
1 – Layout
Il posizionamento dei componenti deve partire da quelli con potenza maggiore, che devono essere posizionati il più possibile vicino alle parti che li accompagnano, in modo tale da creare tracce ad elevata corrente più brevi possibili. Essi devono inoltre mantenere una certa distanza minima dalle tracce su cui viaggiano segnali ad alta velocità, maggiormente sensibili alle interferenze e ai fenomeni di diafonia.
Indicativamente, per il posizionamento dei componenti, si può procedere con il seguente ordine: connettori, componenti di potenza, componenti sensibili, componenti critici, parte restante dei componenti. Tutti i componenti simili andrebbero orientati nella stessa direzione per ridurre la probabilità di errori di saldatura. Sul lato della scheda su cui sono presenti saldature, non posizionare altri componenti vicino ai terminali dei componenti a foro passante (PTH), posizionati sul lato opposto della scheda. I componenti a montaggio superficiale (SMD) andrebbero concentrati sullo stesso lato del PCB; la stessa regola dovrebbe essere applicata ai componenti PTH, semplificando e riducendo i tempi richiesti per l’assemblaggio.
Dopo aver posizionato i componenti, procedere con l’istradamento delle tracce relative ad alimentazione, segnali e terra. Il routing delle tracce dovrebbe assegnare la priorità in base ai livelli di potenza e alla suscettibilità al rumore e alle interferenze. I componenti di potenza dovrebbero utilizzare piani di massa oppure di potenza per una migliore dissipazione del calore, mentre le tracce che portano i segnali dovrebbero essere più corte e rettilinee possibile, evitando che viaggino parallele per lunghi tratti per evitare fenomeni di accoppiamento. In prossimità (o al di sotto) dei pin di alimentazione andrebbero posizionati dei condensatori di disaccoppiamento, in grado di assorbire eventuali picchi spuri dell’alimentazione.
Le tracce con segnali che richiedono un elevato grado di isolamento dovrebbero essere instradate su layer separati, possibilmente ortogonali l'una all'altra con un piano di massa che le separa. Il posizionamento ortogonale delle tracce riduce al minimo l'accoppiamento capacitivo, mentre il piano di massa fornisce una schermatura elettrica. Questa tecnica è largamente utilizzata per ottenere tracce con impedenza controllata, dove l'impedenza caratteristica si mantiene costante in ogni punto (ad esempio, 50Ω). Due tipi molto comuni di tracce ad impedenza controllata sono le microstrip e le stripline, che, pur avendo strutture geometriche differenti, producono risultati simili. Il controllo dell’impedenza, eseguibile attraverso uno dei numerosi strumenti disponibili online, implica spesso la necessità di bilanciare la lunghezza delle tracce. Nei casi limite, ciò può richiedere l’introduzione di opportune “serpentine” realizzate sul PCB, come evidenziato in Figura 1.
Figura 1: introduzione di “serpentine” per bilanciare la lunghezza delle tracce
2 – Separazione
La parte RF di un PCB mobile deve essere opportunamente separata e isolata dalle sezioni di alimentazione e da quelli digitali o analogiche di bassa potenza. I segnali analogici sensibili dovrebbe essere inoltre mantenuti il più possibile distanti dai segnali digitali ad elevata velocità e dai segnali RF. I segnali digitali e quelli analogici dovrebbe inoltre avere, ciascuno, i propri collegamenti a terra.
I circuiti analogici e digitali dovrebbero, ove possibile, essere mantenuti separati. Infatti, i rapidi fronti di salita dei segnali digitali potrebbero creare dei picchi di corrente e generare rumore, due fattori potenzialmente in grado di danneggiare i circuiti analogici. In Figura 2 è visibile un esempio di come la separazione tra sezione analogica e sezione digitale di un PCB possa essere eseguita.
Figura 2: separazione tra sezione analogica e digitale (Fonte: Altium)
3 – Fori di via e fiducial marker
Le tracce ad elevata corrente, soprattutto se attraversano più layer, dovrebbero includere da due a quattro fori di via. Ciò consente di migliorare la dissipazione del calore e di ridurre le perdite sia induttive, sia resistive. L'utilizzo di fori di dimensione maggiore consente alla scheda di sopportare correnti di intensità più elevata e migliora la conduzione del calore. Inoltre, per le tracce attraversate da elevate correnti, è meglio utilizzare più fori invece di un singolo foro.
Come regola generale, ogni lato del PCB dovrebbe includere almeno due fiducial marker. Questi dovrebbero tipicamente avere una forma circolare con diametro di 1 mm (40 mil). Inoltre, i fiducial marker dovrebbero avere lo stesso colore per lo sfondo interno e quindi rimanere compatibili con il rivestimento in rame.
4 – Gestione termica
La gestione termica è un aspetto importante che merita un'attenzione particolare, in quanto una gestione impropria del calore potrebbe degradare o addirittura danneggiare il PCB. Il progettista dovrebbe pertanto consultare i valori di resistenza termica per ciascun componente e determinare quali componenti dissipano più calore. Occorre poi assicurarsi che i componenti più critici siano posizionati a una distanza sufficientemente ampia dai componenti che sviluppano calore.
L'utilizzo di tracce di larghezza maggiore è il primo espediente da utilizzare per combattere la generazione del calore. I componenti di potenza, soggetti al surriscaldamento maggiore, dovrebbero essere posizionati al centro della scheda per favorire la dispersione del calore, rimanendo separati dagli altri componenti caldi. Eventualmente, se le dimensioni del progetto lo consentono, dovrebbero essere prese in considerazione anche ventole di raffreddamento, dissipatori di calore, piani di massa e di potenza uniformi e un adeguato numero di via termici. Potrebbe anche rendersi necessario aumentare lo spessore dei laminati o utilizzare materiali diversi con una migliore resistenza e dissipazione del calore.
5 – Piani di massa
Un piano di massa offre una tensione di riferimento comune, fornisce schermatura, consente la dissipazione del calore e riduce l'induttanza parassita (anche se aumenta la capacità parassita). Idealmente, ogni PCB dovrebbe avere almeno un layer interamente dedicato al piano di massa. I risultati migliori si ottengono quando tale piano è uniforme, cioè privo di interruzioni.
Poiché i piani di massa occupano in genere un’ampia superficie del PCB, la loro resistenza è minima. Alle basse frequenze, la corrente prenderà il percorso con resistenza minore, mentre alle alte frequenze la corrente seguirà il percorso con impedenza minore. I piani di massa e di alimentazione dovrebbero essere simmetrici, centrati e posizionati nei layer più interni del PCB.
6 – Materiali
La tecnologia di fabbricazione dei PCB multistrato è ampiamento utilizzata nelle applicazioni medicali. Durante la fabbricazione di un PCB multistrato, viene applicato un processo sottrattivo per generare i layer del circuito stampato. L'interconnessione tra gli strati è ottenuta attraverso fasi di laminazione, foratura meccanica, ramatura chimica e placcatura in rame. Completano il processo la creazione della maschera di saldatura, il rivestimento protettivo del PCB (conformal coating) e la serigrafia.
Gli attuali PCB multistrato sono eccezionalmente sottili, presentano una larghezza delle tracce e una spaziatura molto ridotte, con una densità di componenti e tracce particolarmente elevata.
7 – Pannello PCB
Un buon progettista dovrebbe includere nello sviluppo il rilascio di un pannello relativo alla fase di assemblaggio. Una volta che il progetto del PCB è stato finalizzato, la fase successiva consiste nell'inviare le informazioni relative al PCB a un'azienda produttrice, insieme a una specifica di progettazione del pannello per garantire che il formato di ricezione dei PCB sia quello previsto. Tali informazioni dovrebbero includere:
- massima dimensione del pannello gestibile dai macchinari di produzione;
- aggiunta di fiducial marker per consentire ai sistemi di allineamento visivo dei macchinari di sapere esattamente dove si trova il PCB. La prassi standard è quella di aggiungere tre fiducial al pannello in tre dei quattro angoli su entrambi i lati del PCB in modo che la macchina possa determinare se il PCB è stato caricato in modo errato;
- introdurre, se richiesto dai macchinari, degli appositi fori (tooling holes) in prossimità dei bordi del pannello, al fine di consentire la lavorazione del PCB;
- curvare gli angoli del pannello in modo tale che, quando i pannelli PCB sono confezionati sottovuoto, gli angoli del pannello non possano rompere i sigilli.
In Figura 3 è visibile un esempio di pannello correttamente progettato.
Figura 3: un esempio di pannello per PCB
26/11/2021