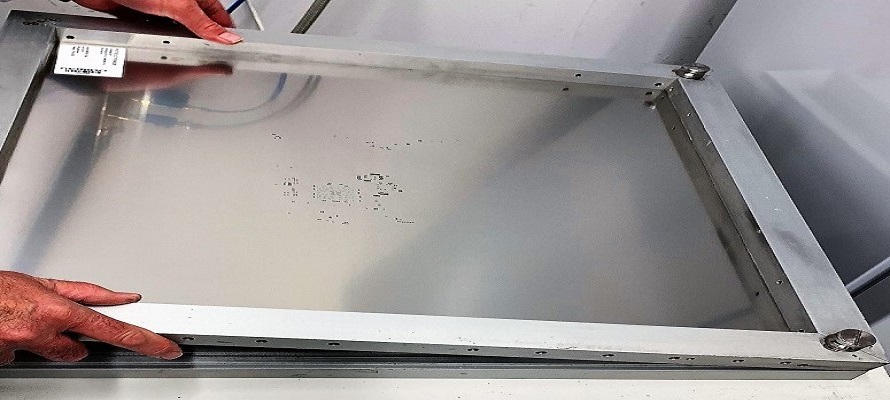
Der Siebdruck ist die marktführende Lösung für die Herstellung elektronischer Leiterplatten und die Aufnahme von SMD-Bauteilen*. Diese Technologie wird regelmäßig angepasst, um den ständig steigenden Anforderungen an die Lötqualität und Kompaktheit der Schaltungen gerecht zu werden. Dieser Artikel vermittelt einen Überblick über die wichtigsten beobachteten Trends.
Welches Prinzip setzt der Siebdruck ein? Hierbei wird eine Schablone, eine Metallfolie mit den Ausschnitten für die Lötinseln, den leitenden Bereichen der Leiterplatte, erzeugt. Anschließend wird diese Schablone (Stencil) auf die Platine aufgelegt und die Lötpaste aufgetragen, indem diese mithilfe des Abziehers auf der Schablone verteilt wird.
Trotz der einfachen Theorie weist diese Technologie eine gewisse Komplexität in der Umsetzung auf: Für ein qualitativ hochwertiges Ergebnis müssen Sie sicherstellen, dass Sie an jeder Stelle der Leiterplatte die richtige Menge Lötpaste aufgetragen haben. Die Qualität der Übertragung hängt von der Geschwindigkeit des Vorgangs, der Qualität der Schablonenfertigung, dem Winkel des Abziehers und den Haftungseigenschaften der gewählten Lötpaste ab. Das Ausschalen ist ein kritischer Schritt.
Ein weiterer Nachteil: Das Herstellungsverfahren der Schablone ist kostenintensiv, da einige der verwendeten Materialien teuer sind, ein hochpräziser Laser zum Schneiden eingesetzt wird und schließlich die Leistung des mechanischen Systems, das die Schablone trägt, eine Rolle spielt.
Vom Konzept zum Schnitt
Die amerikanische Norm IPC 7525B definiert den Standard für die Fertigung einer Schablone, kann aber an die spezifischen Anforderungen des Herstellers angepasst werden. Daraus ergeben sich Dateien, mit denen der Hersteller ein Blech schneidet, dessen Stärke in der Regel zwischen 50 und 300 Mikron liegt. Dieser Schritt erfordert eine Laserschneidemaschine, eine Investition, die sich für einen Bestücker als zu schwerwiegend erweisen würde (in Höhe von mehreren hunderttausend Euro), dies auch dann wenn er ein großer Konsument von Schablonen wäre, was die Spezialisierung einiger Akteure bei der Herstellung von Schablonen erklärt.
Welches Material sollte für Schablonen verwendet werden?
In 80 % der Fälle werden die Schablonen auf 127 Mikrometer starken Edelstahlblechen gefertigt, eine Lösung, die für Karten mit mittlerer Komplexität geeignet ist. Jedoch entwickelt sich der Trend hin zur Entwicklung von elektronischen Leiterplatten mit immer geringeren Abständen, d.h. die Bereiche für die Aufnahme von Komponenten, die immer kleiner werden und enger zusammenrücken.
Um diesen neuen Anforderungen gerecht zu werden, muss der Hersteller immer dünnere Bleche und aufwendigere Materialien als Edelstahl einsetzen. Feine Unterteilungen (unter 0,5 mm) erfordern die Verwendung von DATUM FG (für „fine grain“ auf Englisch), einer Mischung aus Nickel und Edelstahl, deren Eigenschaften das Ausschalen der Form erleichtern. Um noch feinere Unterteilungen zu erzielen, wird die Schablone aus Nickelfolie geschnitten. Obwohl die Verarbeitung viel schwieriger ist, bietet dieses Material eine hohe Ausschalungsleistung. Der Nachteil dieser Materialien besteht in ihrem Preis: eine Nickelschablone kostet doppelt so viel wie eine Edelstahlschablone.
Vor kurzem machte ein neues Material von sich reden: LT123**, das zwischen FG und Nickel angesiedelt ist. Auf einem dünnen Aluminiumrahmen eingesetzt und auf eine Polyesterschablone gespannt, kann eine LT123-Schablone für die Fertigung mehrerer tausend Leiterplatten eingesetzt werden und stellt somit eine Alternative zu Nickel dar. LT123 ist unter anderem in Stärken von 80 bis 150 Mikron erhältlich und bietet außergewöhnliche Ebenheits- und Anhaftung reduzierende Eigenschaften, die es ermöglichen, Schablonen mit sehr hoher Dichte herzustellen. Seine sehr feine Korngröße führt zu einer hervorragenden Freisetzung der Lötpaste. LT123 wurde von einer Vielzahl an Herstellern getestet und eingesetzt. Es wird auch für Schablonen mit einer Stärke von 80 und 100 Mikrometern empfohlen und bietet einen besseren Halt als Schablonen für selbstspannende Rahmen.
Die Auswahl der Lötpaste ist entscheidend
Es existieren verschiedene Arten von Lötpasten, mit oder ohne Bleigehalt. Bleihaltige Lötpasten sind nicht mehr weit verbreitet, außer für bestimmte spezifische Anwendungen, wie z.B. Leiterplatten im militärischen Bereich. Die Wahl der Lötpaste liegt im Ermessen des Herstellers und wirkt sich auf die vorbereitenden Arbeiten aus, die ihn zu Korrekturen an den Schablonen hinsichtlich der Breite der Pads zwingen können.
Unabhängig von den Einschränkungen durch den erforderlichen Lötpastentyp muss der Hersteller auf Kundenwunsch auch die rechteckigen oder quadratischen Lötpads ändern, um z.B. Achtecke oder abgerundete Ecken zu erzeugen.
Übergröße und Gravur
Diese Flexibilität drückt sich auch in der Fähigkeit aus, Übergrößen lokal herzustellen, um eine mehrstufige Schablone zu erstellen.
Einige Komponenten benötigen mehr Lötpaste als andere. Wenn diese auf dem gleichen Leiterplattenniveau einer Leiterplatte montiert werden, hat der Hersteller zwei Möglichkeiten:
– entweder geht er von einem Blech mit der Stärke, die der Mindestmenge an Lötpaste entspricht aus, und klebt oder schweißt ein zweites Blech an bestimmte Stellen, um die Ablagerung von Lötpaste lokal zu erhöhen, wobei beide Bleche im Laserschneideverfahren angefertigt werden müssen;
– oder er geht von einem Blech mit der Stärke aus, die der maximalen Menge an Lötpaste entspricht, und vermindert lokal die Blechstärke durch einen Ätz- oder Hobelprozess.
und erhalten Sie innerhalb von 10 Minuten ein Angebot für Ihr PCBA-Projekt
Welcher Träger sollte für Schablonen verwendet werden?
Hersteller, die sehr große Serien von Karten bestellen (z. B. der Automobilsektor), entscheiden sich für Schablonen, die auf Aluminiumrahmen aufgeklebt werden: Ein Nylon- oder Metallgewebe wird gespannt und auf einen Aluminiumrahmen aufgeklebt, die Schablone wird anschließend auf das zuvor geschnittene Gewebe aufgeklebt. Eine solche Schablone kostet etwas mehr als das Doppelte des Preises einer selbstspannenden Rahmenschablone und ihre Lagerung ist umständlicher.
Diese hohen Kosten veranlassen Bestücker, die Prototypen produzieren (bis zu 1.000 Karten), dazu Schablonen zu verwenden, die auf selbstspannenden Rahmen montiert sind. Diese Art von Rahmen wird in der Siebdruckmaschine platziert, in der ein Bediener zuvor die Schablone befestigt hat. Die Installation der Schablone in einigen selbstspannenden Rahmen stellt ein hohes Risiko für den Bediener dar: 127 Mikrometer sind scharf, wie eine Rasierklinge!
Um das Verletzungsrisiko zu verringern, entwickelte ASM DEK den Vector Guard, eine Schablone für selbstspannende Rahmen mit Metallschutz um das Edelstahlblech. Durch sein relativ geringes Gewicht lässt er sich einfach aufbringen.
Der einzige Nachteil ist der Preis: Sie müssen die Lizenz für die Fertigung von Vector Guard Rahmenschablonen erwerben und die Schablonenmatrizen werden zu einem sehr hohen Preis verkauft.
Es existieren heutzutage viele Lösungen, damit der Siebdruck die Anforderungen eines sicheren und qualitativ hochwertigen Fertigungsprozesses entspricht. Dies schlägt sich auf den Preis von Schablonen nieder, der erheblich sein kann!
* SMD: Surface-mounted device (deutsch: oberflächenmontiertes Bauelement)
** LT123 ist der Name, den Laser Technologie für dieses Material verwendet
Wir danken Alain MILARD, Redaktionsleiter von Electronique MAG und Direktor von Laser Technologie France, für seinen Beitrag zu diesem Artikel.
-oOo-