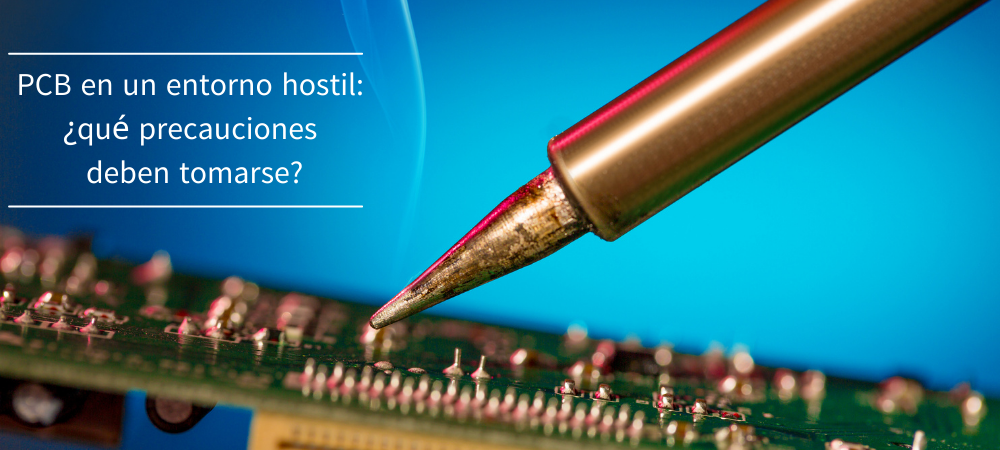
Algunas categorías de dispositivos electrónicos deben funcionar en condiciones especialmente severas, como la niebla salina, la sal, el polvo, la arena o las temperaturas extremas. Para asegurar que el circuito electrónico siga funcionando como en condiciones normales, el PCB debe estar diseñado para tolerar estos eventos sin que resulte dañado. Los PCB utilizados en los sectores de la automoción, industrial o aeroespacial, por ejemplo, están continuamente sometidos a vibraciones, tensiones mecánicas, choques, excursiones térmicas muy amplias, etc..
Aparte de algunas clases de dispositivos electromédicos, son pocos los aparatos electrónicos que funcionan en entornos libres de polvo, vibraciones, humedad y con temperaturas estrictamente controladas. En realidad, es preciso hacer frente a:
- vibraciones y tensiones mecánicas
- variaciones extremas de presión (variaciones en altitud asociadas)
- variaciones extremas de temperatura
- polvo, grasa u otros agentes químicos
- humedad
- radiaciones ionizantes
- interferencias electromagnéticas, tanto radiadas como conducidas
- descargas electrostáticas y transitorios de tensión/corriente.
y obtenga un presupuesto para su proyecto de PCBAs en 10 minutos!
Retos a afrontar
Los principales desafíos a los que se enfrentan los PCB para entornos hostiles pueden resumirse del modo siguiente:
- humedad, polvo y suciedad: para contrarrestar estos factores ambientales, a menudo es necesario tratar el PCB con un proceso especial conocido como revestimiento de conformación. Con él, el PCB se cubre después del proceso de ensamblaje con una fina capa de material protector no conductor, como silicona, acrílico, uretano o p-xileno. El revestimiento permite prolongar la vida del circuito electrónico, protegiéndolo de los contaminantes externos
- altas temperaturas: si el PCB debe funcionar continuamente a temperaturas superiores a la estándar, es mejor utilizar capas con un cobre más grueso (cobre pesado). Unos espesores de cobre superiores a 3 onzas por pie cuadrado normalmente se combinan con la aplicación del revestimiento compatible para proporcionar al panel un elevado nivel de protección, en caso de funcionamiento ininterrumpido a altas temperaturas. El uso de capas con una temperatura de transición vítrea más elevada (Tg), como FR-4 TG140 o TG170), proporciona al PCB una protección adicional frente a la temperatura.
- radiación ionizante: los PCB para aplicaciones aeroespaciales son bombardeados con partículas de diversos tipos, además de la radiación electromagnética generada por el sol y otros cuerpos celestes. Esta radiación puede causar perturbaciones temporales (como el cambio de bits o el borrado de memoria) o daños permanentes a los componentes
- choques y vibraciones, especialmente en aplicaciones de los sectores de automoción y aeroespacial
- corrosión: es uno de los mayores escollos para cualquier pieza metálica. La corrosión se produce cuando el oxígeno y el metal se unen mediante un proceso conocido como oxidación. Esto produce óxido y hace que el metal pierda sus propiedades químicas, descomponiéndose con el tiempo. Los PCB contienen una gran cantidad de metal, por lo que si se exponen al oxígeno están sujetos a la corrosión.
Revestimiento de conformación
Con el fin de evitar los daños causados por los agentes atmosféricos, tras el montaje se aplica al PCB un revestimiento protector no conductor conocido como revestimiento de conformación (Figura 1). Normalmente esto se aplica al PCB para dispositivos de consumo, electrodomésticos y móviles, donde es habitual el funcionamiento en presencia de humedad, polvo u otros factores ambientales adversos. La capa protectora aplicada al PCB permite que la humedad presente en las capas del PCB fluya hacia el exterior, evitando a la vez que los agentes externos lleguen a la placa y sus componentes, comprometiendo su funcionamiento. Además de incrementar la fiabilidad, el revestimiento de conformación prolonga la vida útil del circuito.
Figura 1: aplicación del revestimiento de conformación
Los tipos más comunes de revestimiento de conformación son la silicona, la resina acrílica, el poliuretano y el p-xileno, cada uno de los cuales es capaz de proporcionar un determinado nivel de protección. La silicona, por ejemplo, puede cubrir la gama más amplia de temperaturas y, por tanto, es la mejor opción para aplicaciones con temperaturas extremas. Por otro lado, la silicona tiene un escaso poder de adhesión sobre algunos tipos de sustratos y una menor resistencia química que la resina acrílica. Esta última, debido a su estructura rígida, no es especialmente adecuada en presencia de choques y vibraciones. Los poliuretanos ofrecen una elevada resistencia a la humedad, la abrasión y las vibraciones, y toleran bien las bajas temperaturas, aunque no las altas. En consecuencia, se utilizan principalmente en aplicaciones con temperaturas desde -40°C a +120°C. El p-xileno es un material consistente que ofrece una alta protección, pero resulta caro y, al ser sensible a los contaminantes, debe aplicarse al vacío.
Con respecto a la aplicación del revestimiento conformado del PCB, pueden aplicarse cuatro técnicas: inmersión, revestimiento selectivo automatizado, pulverización y cepillado. Cada una de estas alternativas alcanza el mismo objetivo: cubrir por completo el PCB, incluyendo los bordes afilados y todos los bordes de la placa. Tras la aplicación, el revestimiento de conformación se cura mediante secado al aire, secado en el horno o con luz UV.
Altas temperaturas
La creciente densidad de los componentes del PCB lleva a un inevitable aumento de las temperaturas de funcionamiento, condición que a largo plazo puede comprometer la integridad de las soldaduras o de las propias capas, debido a la expansión y contracción de materiales con diferentes propiedades físicas. Un PCB a temperaturas elevadas debe, por tanto, utilizar un dieléctrico con una temperatura de transición vítrea (Tg) mínima de 170°C. Una regla que se aplica habitualmente es permitir temperaturas de funcionamiento de hasta 25°C inferiores al valor de Tg del material empleado. Además de la elección del material, la elevada temperatura del PCB puede gestionarse extrayendo el calor producido y transfiriéndolo a otras zonas del PCB. Si el componente caliente está montado en la parte superior del PCB y tiene una superficie lo suficientemente amplia, puede instalarse un disipador térmico que pueda extraer el calor primero por conducción (desde el componente al disipador térmico) y luego por convección (desde las superficies del disipador térmico al aire adyacente, más frío).
Si el componente caliente está montado en la parte inferior del PCB y no es posible instalar un disipador térmico, la técnica que normalmente utilizan los diseñadores consiste en insertar una gran cantidad de vías térmicas en el PCB para transferir el calor desde el componente caliente hasta una capa de cobre situada en la parte superior del PCB, desde donde puede transferirse posteriormente a un disipador térmico adecuado. Normalmente, los disipadores térmicos instalados en el PCB son grandes, con superficies aleteadas o corrugadas para incrementar la zona de disipación. Pueden añadirse ventiladores para mejorar la refrigeración por convección forzada, en comparación con la refrigeración por convección natural.
Uno de los métodos utilizados tradicionalmente para contrarrestar los efectos producidos por las altas temperaturas es el uso de la tecnología de cobre pesado. Esto aumenta la corriente máxima que las trazas del PCB pueden transportar y, debido a la menor resistencia, reduce las pérdidas de calor.
Medidas antirradiación
Para misiones espaciales de larga duración, la única opción disponible es el uso de componentes «rad-hard» (endurecidos contra la radiación). Estos componentes son mucho más raros y, en consecuencia, más caros que los componentes estándar. Para misiones espaciales de corta duración (hasta un año), puede permitirse el uso de componentes comerciales estándar, con sujeción a análisis y verificación de su capacidad para resistir la radiación. Esto permite reducir los costes de diseño del equipamiento espacial y ampliar la selección de componentes disponibles para el diseño. Aplicando diferentes técnicas de diseño de hardware, se pueden contrarrestar los efectos producidos por la radiación. A nivel de diseño del PCB, por ejemplo, es importante asegurar una conexión a tierra adecuada de todas las piezas metálicas.
Protección mecánica y corrosión
Al objeto de proporcionar protección contra los choques y las vibraciones, el PCB puede instalarse en un contenedor en el que se vierte resina para encapsularlo por completo. Cuanto más alta sea la capa de resina, mejor será el grado de protección. Salvo que todos los componentes del PCB tengan una altura uniforme, el grosor de la capa de resina variará a lo largo de la placa, confiriendo unos niveles de protección ligeramente diferentes para cada componente. La capa más fina de resina, por tanto, corresponde, en el peor de los casos, al nivel de protección ofrecido a toda la placa. Antes incluso de plantearse el encapsulado con resina, el PCB debe limpiarse a fondo. La contaminación superficial puede afectar negativamente a los niveles de protección ofrecidos por el encapsulado, en especial en casos de resistencia química (ya que proporciona a los productos químicos una vía más fácil de acceso). Además, los contaminantes afectarán negativamente a la capacidad de la resina para absorber los choques físicos y térmicos a causa de la débil formación de capas entre la resina y el PCB, lo que en última instancia conduce a la deslaminación. El hecho de mantener el PCB limpio y seco también garantiza la protección contra el óxido y la contaminación iónica. La corrosión puede evitarse tanto con la aplicación del revestimiento de conformación como mediante acabados superficiales como HASL (el PCB se sumerge en una aleación de estaño y plomo licuado y posteriormente los depósitos de la aleación se nivelan con chorros de aire caliente) y ENIG ( inmersión en oro). La Figura 2 muestra el detalle de un PCB con acabado ENIG.
Figura 2: PCB con acabado ENIG.