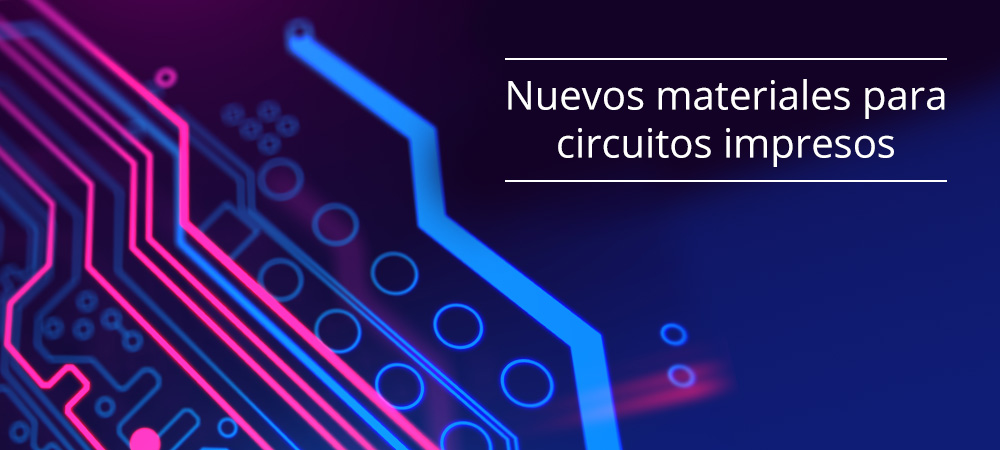
En los últimos años, hemos sido testigos de un progreso significativo en diversas aplicaciones electrónicas, lo que ha propiciado la introducción de tecnologías cada vez más innovadoras. Los sectores en los que se han conseguido los mayores desarrollos incluyen las comunicaciones móviles (smartphones y tabletas), dispositivos portátiles (incluyendo dispositivos de realidad virtual y realidad aumentada) y equipos electromédicos. Se han realizado otros avances importantes en los sectores de automoción y aeroespacial. La confianza derivada de la innovación, en combinación con la disponibilidad de nuevas tecnologías de fabricación, ha permitido la introducción de nuevos materiales para la producción de circuitos impresos aún más delgados, ligeros y, en caso necesario, flexibles, capaces de transmitir señales eléctricas a velocidades y frecuencias cada vez mayores.
La necesidad de nuevos materiales
Los materiales y sustratos tradicionales consisten en tejido de fibra de vidrio, plástico (resina) y cobre. Se utilizan diferentes tipos de resina y vidrio en la fabricación de placas de circuito impreso, y la forma en la que se combinan afecta a las propiedades eléctricas y mecánicas del material. Las dos propiedades eléctricas principales que definen un material son la constante dieléctrica (Dk) y la tangente de pérdida (también conocida como factor de disipación o Df), ambas significativamente dependientes de la temperatura y la frecuencia a que se somete el material o sustrato. La constante dieléctrica especifica la cantidad de carga que pueden soportar dos conductores cuando se les aplica un cierto voltaje. La constante Dk también determina la velocidad a la que fluye una corriente determinada en un conductor. La tangente de pérdida, en cambio, proporciona una medida de la energía electromagnética absorbida por el material dieléctrico.
Las aplicaciones electrónicas más modernas requieren materiales con características diferentes a las ofrecidas por los materiales y sustratos utilizados convencionalmente en la fabricación de circuitos impresos (PCB). Aunque los motivos que determinan la elección son múltiples y dependen estrictamente de la aplicación concreta, una posible lista incluye:
- necesidad de gestionar señales eléctricas con frecuencias cada vez más altas;
- aumento de la densidad de integración de los componentes electrónicos;
- disponibilidad de nuevos paquetes para muchos componentes, con repercusiones en las técnicas de enrutamiento;
- necesidad de minimizar las pérdidas de energía, especialmente en aplicaciones a baja potencia o alimentadas por baterías;
- necesidad de dotar a la PCB de una gestión térmica adecuada a fin de minimizar el calor a disipar;
- necesidad de gestionar la conectividad del dispositivo (normalmente inalámbrico), un aspecto fundamental del diseño de la PCB.
El aumento en la frecuencia de las señales que viajan a través de una PCB parece imparable. Esta característica, junto con unas tensiones de alimentación cada vez más bajas (especialmente en el caso de componentes digitales altamente integrados como MCU, SoC y FPGA) está creando problemas considerables de integridad de la señal. Las aplicaciones de este tipo incluyen tarjetas y equipos de transmisión de fibra óptica, ordenadores y la mayoría de los sistemas integrados equipados con una unidad de procesamiento.
y obtenga un presupuesto para su proyecto de PCBAs en 10 minutos!
Nuevos materiales y sustratos
En base a las consideraciones expresadas en el apartado anterior, podemos identificar los dos factores clave que determinan la selección del material y sustrato más adecuado para la aplicación específica: la máxima potencia y cantidad de calor que puede soportar el circuito impreso. Si bien esta regla es general y aplicable a todo tipo de materiales, pueden obtenerse mayores beneficios gracias a la adopción de materiales innovadores como los siguientes:
- fluoropolímeros: Las PCB fabricadas con sustratos de este material poseen una gran resistencia a la corrosión, a la tensión mecánica y a las altas temperaturas. Asimismo, a nivel mecánico, los fluoropolímeros cuentan con excelentes características de resistencia al desgaste, baja adherencia y prolongada vida útil. Teniendo en cuenta el coste, que no es en absoluto desdeñable, este tipo de material es adecuado para la fabricación de PCB para aplicaciones en la industria médica, farmacéutica y alimentaria;
- poliimida: este material, también conocido como PI, ha obtenido recientemente un gran éxito gracias a la creciente popularidad de las placas de circuito impreso flexibles y rígido-flexibles. Estas PCB están revolucionando diversas aplicaciones electrónicas al resolver problemas de conexión eléctrica, en su momento considerados críticos, de manera eficaz y sencilla, especialmente en términos de fiabilidad. Esto se consigue gracias a su capacidad para flexionarse y envolverse en espacios reducidos o de formas irregulares. A diferencia de las PCB rígidas, las PCB flexibles pueden doblarse sin alterar la transmisión de las señales eléctricas que transportan. Compuestas por una fina película de poliimida depositada sobre un sustrato de trazas conductoras, son de uso generalizado en smartphones, dispositivos portátiles, dispositivos electromédicos y siempre que se necesiten soluciones de cableado flexible adecuadas para espacios reducidos. Además de flexibilidad mecánica, el material así obtenido posee una excelente resistencia al calor y a los agentes atmosféricos. Las PCB rígido-flexibles, un ejemplo de las cuales se muestra en la Figura 1, se obtienen combinando una parte rígida con una parte flexible. Esta solución, que actualmente tiene unos costes superiores a los de las PCB tradicionales, se utiliza en la industria automotriz y motociclista, en el ejército y en el sector aeroespacial;
Figura 1: PCB rígido-flexible.
- adhesivos acrílicos: muy apreciados por su capacidad de mantenerse dúctiles incluso tras la polimerización, estos materiales representan una excelente solución para todas las aplicaciones dinámicas. Los adhesivos acrílicos tienen un coeficiente de expansión superior al de otros materiales utilizados como sustratos de PCB. Además, a temperaturas cercanas a 180 °C, los adhesivos acrílicos comienzan a ablandarse, con la posible delaminación de las capas de las PCB en contacto con trazas conductoras. Si se requiere una alta resistencia al fuego, deben añadirse retardadores de llama químicos al sustrato, con el riesgo de reducir las capacidades dinámicas del material;
- adhesivos epoxi: a diferencia de los anteriores, los adhesivos epoxi polimerizan para formar un material rígido y, por tanto, no son adecuados para muchas aplicaciones dinámicas. No obstante, debido a su relativamente bajo coeficiente de expansión y a su gran poder adhesivo, representan una solución excelente para la construcción de PCB multicapa capaces de soportar altas temperaturas operativas. Los adhesivos epoxi, gracias a su alta resistencia a los productos químicos y a su capacidad para absorber la humedad, se utilizan de forma generalizada como sustratos para PCB cuando los sensores pueden entrar en contacto con la humedad, como en aplicaciones médicas y sanitarias, así como en muchos dispositivos de fitness y portátiles;
- polímeros de cristal líquido: también conocidos como LCP, por sus siglas en inglés, los polímeros de cristal líquido se utilizan a menudo en la fabricación de PCB multicapa, donde la reducción del espesor es un requisito fundamental. Los LCP están hechos de un material extremadamente inerte y no reactivo, con alta resistencia al fuego. Son ligeros y flexibles, con extraordinarias características eléctricas que los convierten en la solución ideal para aplicaciones de alta frecuencia, especialmente cuando debe restringirse el peso y el espesor de la PCB. Los polímeros de cristal líquido también poseen buenas propiedades dieléctricas, con pérdidas y absorción de humedad muy bajas;
- aluminio: los circuitos impresos de aluminio, también conocidos como PCB revestidas de metal o IMS (Insulated Metal Sustrate – Sustrato Metálico Aislado) están compuestos de una fina capa de material dieléctrico térmicamente conductor, pero eléctricamente aislante, estratificado entre una base metálica y una lámina de cobre. La lámina de cobre se graba con el diseño deseado de PCB, mientras que la base metálica tiene la función de absorber el calor producido por el circuito a través de la fina capa dieléctrica. La principal ventaja de las PCB de aluminio es que disipan mejor el calor en comparación con las PCB comunes basadas en material FR-4. Inicialmente diseñadas para aplicaciones electrónicas de alta potencia, las PCB revestidas de metal están aflorando como una solución ideal para soportar sistemas de iluminación LED de gran luminosidad, tanto en el sector de consumo como en el de la automoción. La Figura 2 muestra una PCB de aluminio para aplicaciones en el campo de la iluminación LED ultraluminosa.
Figura 2: Ejemplo de PCB revestida de metal.
Los nuevos materiales, capaces de proporcionar un rendimiento superior en comparación con los tradicionales, están sujetos a un desarrollo continuo y creciente, debido a la capacidad de mejorar varios aspectos relacionados con la integridad de la señal. Un valor más bajo de Dk mejora el control de impedancia, la diafonía, la fluctuación y la desviación de la señal. Un valor más bajo de Df, por otro lado, ayuda a mejorar los tiempos de elevación y caída y la atenuación total.