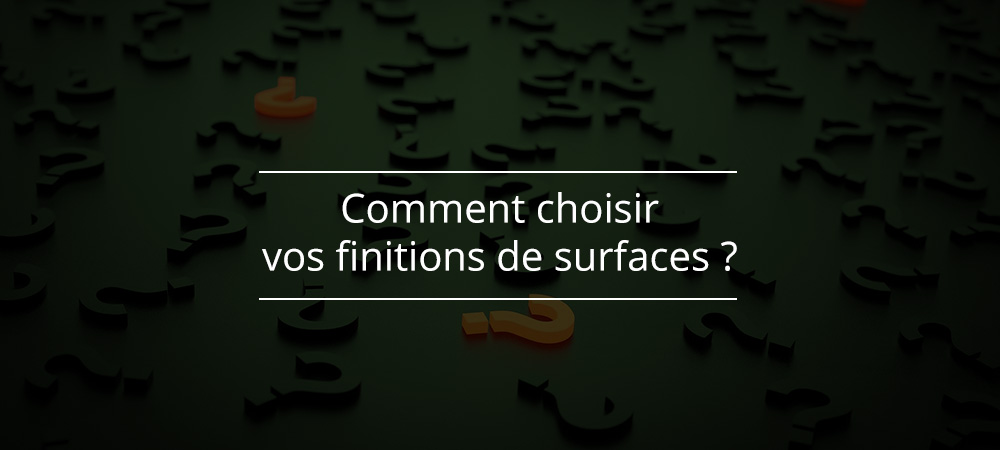
Afin d’empêcher l’oxydation du cuivre et d'assurer une bonne soudabilité des composants, les surfaces d'un circuit imprimé doivent passer par une étape de finition. Voici un tour d'horizon et quelques conseils pour vous aider à choisir la méthode de finition la plus adaptée à votre application.
La qualité d’une brasure résulte de la qualité initiale (vis-à-vis du brasage) du circuit imprimé utilisé et des composants électroniques qui sont montés sur les surfaces ; cette qualité est appelée la brasabilité. La finition des circuits imprimés - par une métallisation ou par tout autre procédé - a pour objectif de préserver la brasabilité du métal de base et de fournir la meilleure interface possible avec le joint brasé.
Si votre application bénéficie d’une exemption RoHS qui vous permet de continuer à utiliser du plomb, vous pouvez conserver l’étain-plomb qui a servi de masque de gravure lors de la fabrication du PCB ; après refusion, le SnPb constitue une bonne finition.
Mais la finition de surface prédominante reste la méthode Hot Air Solder Leveling (HASL), qui consiste à réaliser un dépôt sélectif d’étain-plomb par immersion dans un bain d’alliage en fusion puis nivelage à l’air chaud. Cette finition soudable est depuis longtemps reconnue comme la plus robuste et permettant d'obtenir des assemblages cohérents ; elle affiche cependant ses limites face à l'augmentation constante de la complexité des circuits et de la densité des composants.
Les revêtements alternatifs utilisent l'électrolyse ou l'immersion
Suite à la mise en application en 2006 de la directive RoHS, la disparition du plomb dans les circuits imprimés a entraîné l'apparition de nombreuses alternatives en matière de finition. Celles-ci permettent, d'une part d'éviter l'utilisation du plomb dans l'ensemble du processus, d'autre part de réaliser des revêtements minces et des pas plus fins.
Organic Solderability Preservative (OSP) ou passivation organique
La première méthode que nous considérerons est la passivation organique, appelée également OSP (Organic Solderability Preservative). L'OSP est un procédé de trempage ou de pulvérisation d'un composé organique à base d’eau qui se lie sélectivement au cuivre et fournit une couche organométallique protectrice.
Avantages
Le procédé est simple et peu onéreux ; il n’utilise pas de matériaux toxiques et consomme moins d’énergie que les autres procédés ; il produit des surfaces bien planes et assure une mouillabilité suffisante lors de refusions.
Inconvénients
La durée de stockage est faible, le nombre de refusions est limité, et la fiabilité des assemblages n'est pas exceptionnelle.
Les autres finitions que nous étudierons se font par métallisation de la surface du cuivre à l'aide d‘argent, d‘étain ou d‘or. Cette métallisation est réalisée soit par dépôt chimique, soit par dépôt électrolytique. Il est à noter que la présence de ces métaux, même en faible quantité, va modifier la nature de l‘alliage d‘assemblage final.
Hot Air Levelling ou étamage par nivelage à air chaud
L‘étamage par nivelage à air chaud (Hot Air Levelling) est une variante du HASL qui n'utilise pas de plomb : le circuit imprimé, préalablement humecté avec des produits liquides, est plongé dans un bain d'étain-cuivre liquide puis séché à l'air comprimé afin de supprimer l’excédent d’alliage.
Avantages
La brasabilité et la mouillabilité sont bonnes et le coût de production est faible.
Inconvénients
La planéité ne permet pas l'assemblage de composants à pas fin et l'étain diffuse dans le cuivre.
ENIG (Electroless Nickel/Immersion Gold)
Le procédé ENIG (Electroless Nickel / Immersion Gold) consiste à réaliser un dépôt de nickel par voie autocatalytique puis un dépôt par immersion d’une très fine couche d’or. Le nickel protège le cuivre et constitue la surface à laquelle les composants seront soudés.
Il empêche également la diffusion du cuivre dans l'or dont la fonction est de protéger le circuit durant le stockage. Il existe deux variantes du procédé :
– dans certains cas, le dépôt sélectif de nickel-or peut être réalisé après dépôt du vernis épargne de brasure ;
– dans d'autres, ce dépôt intervient avant celui du vernis épargne sur l’ensemble du cuivre externe.
La norme de référence est l'IPC-4552 Specification for Electroless Nickel/Immersion Gold (ENIG) Plating for PCBs.
L’ENIG convient parfaitement pour des circuits multicouches ou qui comportent des composants à pas fins. Il est utilisé pour des circuits imprimés avec une insertion SMD.
Avantages
Un dépôt uniforme et parfaitement plat, une bonne mouillabilité, la possibilité de multiples refusions, une longue durée de stockage.
Inconvénients
Le coût de production élevé et le risque de défauts liés à l'oxydation du nickel avant l'immersion dans l'or (appelés black pad) qui posent des problèmes lors de la brasure de BGA.
ENEPIG (Electroless Nickel / Electroless Palladium / Immersion Gold)
L'ENEPIG est un procédé dérivé de l’ENIG ; la couche intermédiaire de palladium permet d'éviter l’oxydation du nickel avant l'immersion dans l'or (qui génère des défauts appelés black pad).
La norme de référence est l'IPC-4556 Specification for Electroless Nickel/Electroless Palladium/Immersion Gold (ENEPIG) Plating for PCBs.
Avantages
Cette finition supporte parfaitement de multiples refusions, peut garantir une bonne brasabilité et permet de réaliser des assemblages fiables ; elle convient pour le câblage aluminium et surtout, elle permet de maîtriser la soudure thermosonique de fils d’or.
Inconvénients
Le coût global est élevé, la brasabilité est réduite lorsque la couche de Palladium est épaisse, et la mouillabilité n'est pas excellente.
Tin plating ou étain chimique
L'étain chimique (Tin Plating) est une finition métallique déposée par une réaction de déplacement chimique appliquée directement sur le cuivre de la carte. Ce procédé ancien a connu des modifications depuis quelques années et les performances de la finition ont été améliorées. La norme de référence est l'IPC-4554 Specification for Immersion Tin Plating for PCBs.
L’étain chimique revient à la mode et devrait devenir à court terme la finition préférentielle alternative à l'ENIG pour les applications CMS. Cette finition est compatible avec des assemblages par connexions insérées en force et des assemblages de composants à pas fins.
Avantages
Le dépôt est uniforme et présente une bonne mouillabilité, de multiples refusions sont possibles ; la finition est idéale pour les connecteurs press-fit et les cartes fond de panier.
Inconvénients
L’épaisseur est difficile à contrôler ; l'étain s’oxyde très facilement et peut développer des "moustaches" (whiskers), minuscules filaments qui peuvent provoquer des courts-circuits ; le stockage est limité à 6 mois.
Silver Plating ou dépôt d’argent chimique
Le dépôt d'argent chimique (Silver Plating) est obtenu en plongeant le circuit dans une solution acide contenant des sels d’argent. La norme de référence est l'IPC-4553 Specification for Immersion Silver Plating for PCBs.
Avantages
Un dépôt uniforme, une bonne mouillabilité, la solution idéale pour le collage de fils d'argent.
Inconvénients
Une faible durée de stockage, l'oxydation en présence de soufre ou d'oxygène.
Hard Electrolytic Gold ou le procédé de l’or dur
Enfin, l’or dur (Hard Electrolytic Gold) est un procédé électrolytique au cours duquel une couche d’or est plaquée sur une couche de nickel. À la différence du procédé ENIG, l'épaisseur de la couche d'or peut être ajustée en jouant sur la durée du cycle de plaquage.
Avantages
L'or dur est extrêmement durable et est le plus souvent appliqué aux zones à forte usure telles que les doigts de connecteur de bord et les claviers ; plus généralement, cette finition est utilisée lorsque les surfaces exposées de la carte sont soumises à des frottements ; contact mobile, frottement, enfichage-débrochage, etc.
Inconvénients
L'or dur n'est généralement pas appliqué aux zones soudables, en raison de son coût élevé et de sa brasabilité relativement faible.
Comment faire son choix?
Quelle que soit le type de circuit imprimé et les spécifications attendues, nous vous suggérons de prendre en compte des critères suivants :
- le coût
- l’environnement d'utilisation du produit fini
- la finesse des pas
- la présence ou non de plomb
- la possibilité de hautes fréquences (pour les applications de radiofréquence)
- la durée de stockage
- la résistance aux chutes et aux chocs
- la tenue en température
- le volume à produire et la cadence.
Pour en savoir plus, vous pouvez consulter les normes IPC-2221B "Norme Générique de Conception du Circuit imprimé" et IPC-6012 "Spécification de qualification et de performance des circuits imprimés rigides".