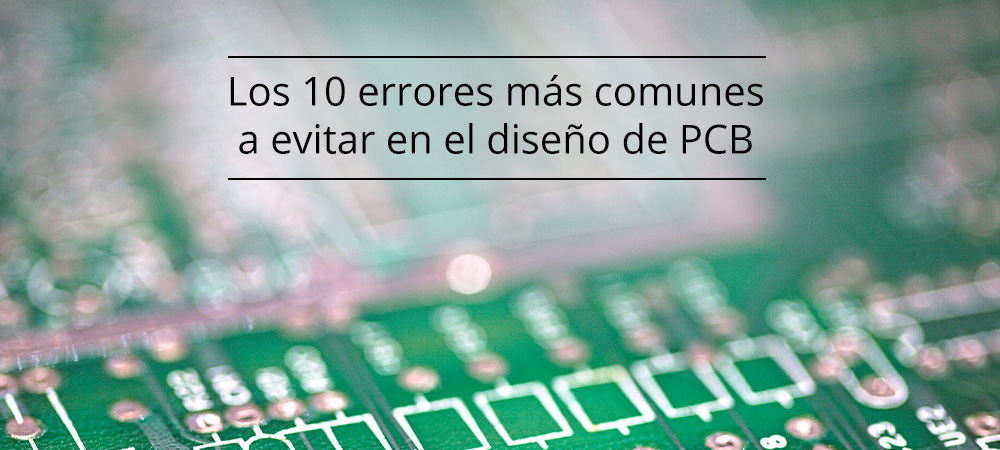
La tarjeta de circuito impreso, o PCB, representa el corazón y el alma de cualquier circuito electrónico. Como responsable de la conexión eléctrica entre los componentes y de la interconexión del dispositivo con el mundo exterior, es evidente que incluso el más pequeño error de diseño puede causar retrasos o costes adicionales durante la fabricación, o incluso conducir a disfunciones o a un fallo total del circuito. Las últimas y más innovadoras herramientas de diseño permiten a los fabricantes de PCB reducir significativamente los costes de producción, en comparación con el pasado. En ocasiones, sin embargo, los costes de fabricación pueden aumentar debido a errores cometidos en la fase de diseño del PCB. Dicho esto, cabe señalar que los errores no son improbables incluso para los diseñadores de PCB más experimentados, así que nuestro consejo es seguir unas sencillas reglas para evitar repetir los diez errores de diseño más comunes, que describiremos ahora.
1 – Geometría incorrecta de la traza
Las trazas del PCB son responsables de transmitir señales eléctricas entre los diversos componentes del circuito, respetando precisas limitaciones relativas a velocidad, intensidad de la corriente y frecuencia de la señal. En este contexto, la geometría de cada traza juega un papel esencial. En concreto, es necesario dimensionar apropiadamente el ancho y el grosor de cada traza. Cuando la corriente que fluye por una traza supera el valor indicativo de 0,5 A, podemos hablar de una línea de transmisión de energía o de una línea de alta corriente. En este caso, ya no es posible utilizar el ancho estándar que se usa en los circuitos de baja potencia, sino que deberá dimensionarse adecuadamente con el empleo, por ejemplo, de calculadoras basadas en la norma IPC-2221 o posteriores para las trazas internas (stripline) y externas (microstrip). Debe tenerse en cuenta asimismo que las trazas situadas en las capas externas del PCB pueden transmitir, con el mismo grosor, una corriente más elevada, ya que pueden aprovechar el mayor caudal de aire y una mayor disipación térmica. El ancho de la traza depende de la cantidad de cobre utilizado en esa capa. Además del ancho, el grosor de cada traza también debe dimensionarse adecuadamente. La mayoría de fabricantes de PCB permiten elegir entre varios grosores de cobre, desde 0,5 oz/ft2 hasta 2,5 oz/ft2 y mayores. Muchos diseñadores a menudo eligen el valor de grosor estándar, correspondiente a una onza de cobre (1 oz equivale a 35 µm). Sin embargo, este valor puede no ser suficiente para las pistas de alta energía, donde normalmente se utiliza un grosor de 2 o 3 onzas. La ventaja de un mayor grosor es que presenta una menor resistencia al paso de corriente, con la consiguiente mejora de la disipación térmica. Las desventajas están relacionadas con un mayor peso y la necesidad de un mayor aislamiento de la traza.
2 – Diseño inadecuado
Con el continuo aumento de la demanda de placas de circuito impreso todavía más pequeñas, los diseñadores se ven forzados a usar componentes con menor huella y a reducir la distancia entre componentes. Si se utiliza un diseño ineficiente, existe el riesgo de encontrarse con problemas de conexión o de incumplimiento. Esto es especialmente cierto cuando se utilizan componentes con un menor paso y un mayor número de pasadores. Para garantizar la funcionalidad deseada, es muy importante seleccionar una técnica de diseño que se adapte a las necesidades de un circuito en concreto. Resulta muy conveniente dejar suficiente espacio en el PCB para los componentes adicionales (o alternativas a los existentes), que puedan ser necesarios en un futuro inmediato. En caso de que no se utilicen estos componentes adicionales, siempre es posible retirarlos antes de la fabricación.
y obtenga un presupuesto para su proyecto de PCBAs en 10 minutos!
3 – Posición incorrecta de los condensadores de desacople
Los condensadores de desacople son necesarios en las líneas de suministro eléctrico del PCB para garantizar un suministro eléctrico estable sin transiciones ni oscilaciones a todos los componentes de la placa. Es absolutamente necesario que estos condensadores estén siempre conectados en paralelo con el suministro eléctrico y colocados lo más cerca posible de los pasadores de los componentes que requieren electricidad. La línea eléctrica procedente de la fuente de energía debe enrutarse adecuadamente en el PCB, a fin de que llegue al condensador de desacople antes de alcanzar el pasador que precisa una tensión estable. Téngase en cuenta que, de otro modo, la función de desacople no puede funcionar adecuadamente. De hecho, todos los reguladores de tensión utilizan un circuito de realimentación que puede oscilar si no está adecuadamente estabilizado.
4 – Errores en el Landing Pattern
Aunque los términos Landing Pattern y Footprint se utilizan con frecuencia de manera indistinta, existe una sutil diferencia entre ellos. De manera más precisa, los Landing Patterns se refieren al tamaño de los pads, y para cada componente, deberían tener siempre una superficie ligeramente mayor que la de la huella correspondiente. Incluso un error de medio milímetro en la medición de la distancia pad-a-pad puede resultar fatal en la soldadura durante el proceso de fabricación, causando desalineaciones entre los componentes y el PCB. Las mejores herramientas de software CAD para PCB cuentan con una gran colección de catálogos que incluyen tanto el símbolo esquemático como el Landing Pattern para cada componente. Si se utiliza un componente no incluido en estos catálogos, es necesario añadir manualmente tanto el símbolo eléctrico como el Landing Pattern del PCB. En esta fase, la posibilidad de cometer algún error no es infrecuente. Por ejemplo, si la distancia entre dos pads es inferior a un milímetro, los pasadores no se alienarán adecuadamente, imposibilitando la soldadura. La Figura 1 muestra las dimensiones relativas a los Landing Patterns de un componente con un paquete PG-TQFP-64-19, obtenido directamente de la ficha técnica. Normalmente, los fabricantes de componentes electrónicos siguen los requisitos incluidos en la norma IPC-7351B (« Generic Requirements for Surface Mount Design and Land Pattern Standards »).
Figura 1: Ejemplo de especificación de un Landing Pattern (Fuente: NXP).
5 – Excesiva confianza en el enrutamiento automático
Para los PCB que no revisten demasiada complejidad, algunos diseñadores tienden a confiar en la funcionalidad de enrutamiento automático, que actualmente ofrece la mayoría de herramientas de diseño de PCB. Sin embargo, el enrutamiento automático tiende a ocupar una zona mayor de la deseable en el PCB y a crear orificios de paso más grandes que los que pueden obtenerse con el enrutamiento manual. Es un hecho que el número de pistas del PCB, junto con en número de orificios de paso, afecta directamente al coste de fabricación del PCB.
6 – Vías ciegas o enterradas
Los orificios de paso son muy adecuados, ya que permiten solucionar muchas situaciones complejas de enrutamiento y mejorar el intercambio térmico del PCB. Sin embargo, deben emplearse con precaución y buen criterio. Las vías ciegas (tipo “1” en la Figura 2) deben utilizarse para conectar una capa externa con una interna, mientras que las vías enterradas (tipo “2” en la Figura 2) se emplearán para conectar dos capas internas entre sí. Las vías de orificios pasantes (tipo "3" en la Figura 2), en cambio, deben utilizarse únicamente para conectar las dos capas externas del PCB y, posiblemente, algunas capas internas. Para crear un orificio de paso, es necesario especificar el tamaño total, el tamaño del orificio, las tolerancias y otros atributos. Pueden crearse a partir de plantillas con la posibilidad de definirse sobre la marcha. Hay que tener en cuenta que las vías ciegas y enterradas implican un mayor coste de producción, por lo que es aconsejable planificar su uso de antemano con el fin de respetar el presupuesto asignado al PCB.
Figura 2: Tipos de orificios vía (Fuente: Altium).
7 – Longitud excesiva de la traza
Las trazas que transmiten señales de alta velocidad deben ser lo más cortas y rectas posible. Si la longitud es excesiva, existe la posibilidad de que se planteen problemas graves como la reflexión de la señal (con consecuencias directas en la integridad de la señal), mayor sensibilidad a la interferencia electromagnética (IEM) y, obviamente, mayores costes. Si la longitud de una traza supera una décima parte de la longitud de onda de la señal que la cruza, podemos hablar de una línea de transmisión. En este caso, además de la longitud, resulta esencial realizar un cálculo de impedancia (utilizando una de las muchas herramientas específicas, disponibles también en línea) a fin de garantizar el acoplamiento de la impedancia y evitar la pérdida de potencia de la señal.
8 – Interferencia electromagnética (IEM)
La interferencia electromagnética a menudo está causada por un diseño incorrecto del PCB. Para reducir la IEM en un PCB, se recomienda agrupar los elementos según su funcionalidad, como bloques analógicos y digitales, secciones de potencia, circuitos de baja velocidad, circuitos de alta velocidad, etcétera. Además, es necesario reducir, o más bien eliminar, los ángulos rectos de las trazas, y utilizar contenedores metálicos y cables apantallados para absorber la interferencia.
9 – Diseño incorrecto de la antena
En caso de que el PCB incluya antenas para la comunicación inalámbrica, los diseñadores deberán extremar las precauciones para no cometer errores de diseño. Al objeto de maximizar la transmisión de potencia, en primer lugar es necesario adaptar la impedancia entre el transceptor y la antena. Normalmente, la línea de transmisión que conecta el transceptor con la antena debe tener una impedancia de 50 Ω. Para un ajuste preciso de la impedancia, debe colocarse entre la antena y el transceptor un filtro sintonizador Pi (LC) o cualquier otro circuito compatible.
10 – Revisión insuficiente del proyecto
A menudo subestimada, la revisión del diseño es en realidad uno de los elementos más importantes en el proceso de desarrollo del PCB. Las revisiones periódicas del proyecto permiten verificar la conformidad con los elevados requisitos del proyecto, las funciones asignadas al PCB y las interconexiones entre los diversos circuitos. Esto permite a los diseñadores evitar, o detectar de antemano, los errores de diseño más comunes. una revisión entre pares, realizada por otros miembros del equipo de desarrollo con frecuencia puede identificar los errores que el diseñador no había detectado anteriormente.