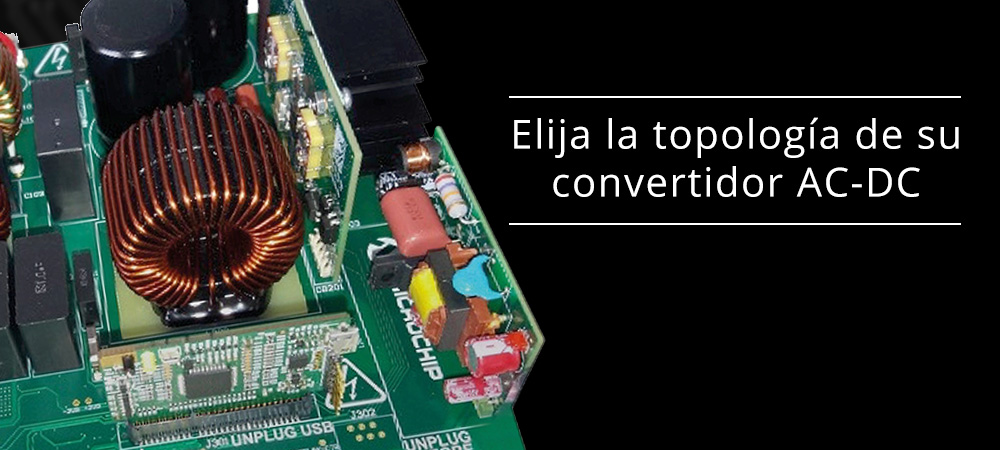
Cuando los diseñadores de sistemas de alimentación inician el diseño de un nuevo convertidor de potencia AC-DC, se enfrentan inmediatamente a la elección decisiva de la topología. En general, los proveedores de circuitos integrados de regulador de potencia soportan al menos siete topologías diferentes. Cada una de ellas presenta sus propias ventajas e inconvenientes. ¿Cuál es, pues, la mejor manera de elegir la topología para una aplicación determinada?
Este artículo proporciona directrices para una evaluación a fondo que permite limitar la gama de topologías seleccionadas. Con estas directrices, los diseñadores verán que pueden racionalizar su investigación y elegir una topología inteligente de manera más eficaz al inicio de un nuevo proyecto.
Sin embargo, cualquier diseñador de alimentación experimentado lo puede confirmar: la historia está plagada de ejemplos de proyectos fallidos o aplazados, cuyo fracaso puede atribuirse directamente a las decisiones adoptadas al comienzo del proyecto. Antes de presentar la guía de buenas prácticas para la evaluación de topología, conviene comprender en primer lugar los factores que desacreditan los modelos de convertidor AC-DC en su fase inicial.
Las causas de error de juicio en relación con la topología
Según la experiencia de este autor, las causas más extendidas de fracaso de diseño en los proyectos de convertidor AC-DC tienen sus raíces en un error de juicio de orden técnico o en un comportamiento humano.
Desde el punto de vista técnico, es probable que los diseñadores sin experiencia utilicen una norma empírica rudimentaria basada en la carga eléctrica máxima que el convertidor debe soportar. La potencia nominal es obviamente un parámetro esencial, pero no es de ninguna manera el único afectado por la elección de la topología.
El tamaño y el peso del sistema, su coste, la eficacia energética, la eficacia térmica, la complejidad y el nivel de interferencia electromagnética (electromagnetic interference o EMI) son todos factores que pueden optimizarse por el diseñador con una buena topología. Asimismo, hay que reconocer que estos factores son interdependientes. Por ejemplo, una compleja topología de conmutación de voltaje cero (Zero-Voltage Switching o ZVS) producirá efectos EMI mucho menos graves que un esquema de conmutación más simple. Las decisiones que se hagan al principio de un diseño no solo deben reflejar las especificaciones técnicas del diseño del producto, sino también la capacidad del equipo de desarrollo y el tiempo de diseño disponible. Por ejemplo, para un equipo de desarrollo con una gran experiencia en la atenuación de EMI y el cumplimiento de la compatibilidad electromagnética (por ejemplo, electromagnetic compatibility o EMC) sería positivo utilizar una topología de conmutación en lugar de su compleja alternativa ZVS.
El otro factor que en la práctica socava la selección de la buena topología es la naturaleza humana. Es habitual, y en definitiva comprensible, precipitar la elección inicial de la topología con el fin de avanzar más rápidamente hacia el desarrollo material. A menudo esto se debe a que un gerente puede ver un prototipo funcional y verse deslumbrado por él: es un signo visible de progreso en el proyecto. También hay que reconocer que diseñar circuitos y construir planos es mucho más entretenido e interesante que realizar búsquedas documentales de topologías.
Otra debilidad humana común para los ingenieros trastoca proyectos de concepción de sistemas de alimentación: Una preferencia para la solución solitaria de problemas técnicos, a expensas de la colaboración y el trabajo en equipo. La elección de una topología requiere generalmente una ponderación cuidadosa de los diferentes arbitrajes posibles a nivel del sistema. Por ejemplo, una decisión que reduzca el coste de la nomenclatura producida (Bill-of-Materials o BoM) pero aumente el tamaño y el peso de un convertidor podría alterar los acuerdos logísticos y aumentar los gastos de envío del producto final en su conjunto. Estos factores superan con creces el poder de gestión del servicio de ingeniería. Una visión holística de todos los costes a lo largo de todo el ciclo de vida del producto podría ayudar al ingeniero de diseño a elegir mejor los componentes al estar más informado.
En general, la experiencia sugiere que hay que tener en cuenta los fracasos, ya que un entorno comercial más amplio puede conducir a retrasos en el proyecto e incluso a anulaciones.
Evitar errores iniciales en los proyectos de diseño de alimentos
La pregunta que surge de la discusión anterior es cómo evitar este tipo de error.
La respuesta obvia es hacer lo contrario de estos enfoques incorrectos:
- Colabore con sus compañeros de otros servicios para obtener información pertinente sobre todos los factores que intervienen en la elección de la topología.
- Realice una investigación detallada de todas las topologías aplicables, evalúe todos los factores afectados por esta elección.
Esta segunda recomendación puede parecer ambiciosa, debido a las numerosas opciones de topologías que hay que analizar. De hecho, no es tan desalentador como puede parecer a primera vista, ya que para cada evaluación de alimentación determinada es generalmente posible limitar la elección a dos o tres topologías adecuadas.
La tabla 1 tiene por objeto facilitar esta evaluación de primer nivel: proporciona una nota para cada topología en relación con cada factor que debe tenerse en cuenta, en la que la mejor topología tiene una nota de 5 y la peor una nota de 1. Las notas proporcionan una indicación aproximada, y los diseñadores de alimentación experimentados podrían discutir una nota u otra. Sin embargo, en general, el cuadro constituye una guía útil para orientar el proceso de evaluación y para fundamentar los debates de los diseñadores sobre las posibles compensaciones con los colegas.
Nivel de potencia |
Topología |
Eficacia |
Complejidad |
EMI |
Tamaño/Densidad de potencia |
Coste |
Factor de potencia |
< 100 W |
Flyback |
2 |
5 |
2 |
5 |
5 |
Ningún PFC < 75 W, CrCm > 75 W |
100-150 W |
Flyback |
2 |
5 |
2 |
5 |
5 |
CrCm |
Forward |
3 |
4 |
3 |
3 |
3 |
CrCm |
|
150-200 W |
Forward |
2 |
4 |
3 |
3 |
3 |
CrCm |
LLC resonante |
4 |
1 |
5 |
4 |
1 |
CrCm |
|
200-250 W |
Forward |
2 |
4 |
2 |
2 |
4 |
CrCm/CCM |
Forward 2 switch |
3 |
3 |
3 |
3 |
3 |
CrCm/CCM |
|
LLC resonante |
4 |
1 |
5 |
4 |
1 |
CrCm/CCM |
|
250-300 W |
Forward |
2 |
4 |
2 |
2 |
4 |
CrCm/CCM |
Forward 2 switch |
3 |
3 |
3 |
3 |
3 |
CrCm/CCM |
|
LLC resonante |
4 |
1 |
5 |
4 |
2 |
CrCm/CCM |
|
Half Bridge |
4 |
2 |
3 |
2 |
2 |
CrCm/CCM |
|
300-400 W |
Forward 2 switch |
2 |
3 |
2 |
3 |
4 |
CCM |
LLC resonante |
5 |
1 |
5 |
5 |
2 |
CCM |
|
Half Bridge |
4 |
2 |
3 |
3 |
2 |
CCM |
|
400-500 W |
LLC resonante |
5 |
2 |
5 |
5 |
2 |
CCM |
Half Bridge |
4 |
3 |
3 |
3 |
3 |
CCM |
|
500-600 W |
Half Bridge |
3 |
3 |
3 |
3 |
3 |
CCM/entrelazado |
Full Bridge |
5 |
2 |
3 |
2 |
2 |
CCM/entrelazado |
|
600-800 W |
Full Bridge |
4 |
2 |
3 |
3 |
2 |
Entrelazado |
Conmutación de fase ZVT |
5 |
1 |
4 |
4 |
1 |
Entrelazado |
|
> 800 W |
Conmutación de fase ZVT |
5 |
1 |
4 |
4 |
1 |
Entrelazado en 3 fases |
Tabla 1: Clasificación de varias topologías de convertidores AC-DC en la columna de corrección de factor de potencia, CrCm = modo de conducción crítico (Critical Conduction Mode) y CCM = modo de conducción continua (Continuous Conduction Mode)
Impacto de las opciones de nueva tecnología
Más allá de la elección de la topología, existe otro elemento importante en la búsqueda del diseñador antes de que se embarque en la implementación del hardware: El descubrimiento de nuevos componentes o tecnologías que han cambiado el escenario desde la implementación de proyectos de diseño anteriores.
Actualmente, por ejemplo, muchos diseñadores de convertidor AC-DC deberían considerar la utilización de los nuevos componentes de alimentación de banda ancha de carburo de silicio (SiC) o nitruro de galio (GAN), que soportan conmutaciones mucho más rápidas que los equivalentes de silicio y pueden funcionar a temperaturas más elevadas.
Si se da prioridad al diseño a un tamaño y peso reducidos y a una densidad de potencia elevada, estos aspectos resultan particularmente interesantes. El SiC MOSFET, actualmente disponible en cantidades de producción en proveedores tales como STMicroelectronics, ROHM Semiconductor y Microsemi (una empresa Microchip en la actualidad), permite utilizar condensadores e inductores más pequeños, lo que reduce el tamaño del conjunto completo del convertidor. La máxima temperatura de funcionamiento de los aparatos de SiC también puede permitir en algunos casos al diseñador eliminar un ventilador o un disipador térmico que hubiera sido necesario en un diseño de silicio en MOSFET, incluso en una caja muy congestionada con una circulación limitada de flujo de refrigeración del aire.
Los transistores X-Gan GAN HEMT (High Electron Mobillity Transistors) de Panasonic ofrecen ventajas similares en la tarjeta de diseño de referencia GaNdalf de Future Electronics (véase la ilustración 1). Este diseño muestra la topología bridgeless de tipo totem-pole en la fase de corrección de factor de forma (Power factor de corrección o PFC) de una alimentación AC-DC < 1 kW. El uso de transistores GAN permite al circuito alcanzar una eficacia superior al 99 % en la fase de PFC.
Ilustración 1: La tarjeta de diseño de referencia GaNdalf para alimentación AC-DC de Future Electronics
Otro concepto de producto reciente y significativo en el diseño actual del convertidor AC-DC es la integración del controlador primario y secundario en un circuito integrado único, para los convertidores que suministran menos de 80 W. Este enfoque es posible gracias a un circuito integrado de controlador de potencia innovador, desde Monolithic Power Systems. El MPX2001 ofrece una solución plenamente integrada a los diseños de convertidor de Flyback.
Se trata de un controlador Flyback que dispone de una regulación primaria y secundaria integrada y de un piloto de recuperación sincrónica dotado de un aislamiento capacitivo. Gracias al MPX2001, es posible reducir el nivel de complejidad del sistema, ya que no se necesita ningún bucle de retorno. Esto también reduce el coste total del BoM. Al mismo tiempo, es posible hacer coincidir perfectamente un rectificador síncrono con la señal de control del lado primario MOSFET. Con esta característica, el rectificador puede funcionar con seguridad en el modo de conducción continua, ayudando a aumentar la eficiencia general y proporcionando más flexibilidad de diseño.
Ilustración 2: El kit de evaluación MPX2001, un modelo pequeño que sirve de demostración para un adaptador o cargador de ordenador o de teléfono inteligente. (Crédito imagen: Monolithic Power Systems)
La elevada eficacia de las empresas de transformación AC-DC basadas en el MPX2001 queda demostrada por el kit de evaluación EVKT-MPX-2001-45-PD de Monolithic Power Systems (véase la ilustración 2). Se trata de un modelo para un adaptador USB de potencia de 45 W destinado a transmitir energía a través de una conexión USB tipo-C. Supera con creces los requisitos de eficiencia del nivel VI del Departamento de Energía de los Estados Unidos y de las normas europeas CoC Tier 2. El consumo de energía sin carga es < 0,075 W.
Combinando tecnologías de componentes mejoradas, una reflexión global sobre las ventajas y desventajas contrastadas de cada topología de convertidor y la comprensión de las necesidades de otros servicios más allá del laboratorio de ingeniería, los diseñadores de sistemas de alimentación pueden ofrecer la mejor oportunidad de éxito a sus proyectos, pero también la oportunidad de alcanzar o superar las especificaciones de diseño del producto final.
Artículo redactado por Riccardo Collura.
Northern Europe Power Specialist Field application Engineer, Future Electronics
www.futureelectronics.com
y obtenga un presupuesto para su proyecto de PCBAs en 10 minutos!