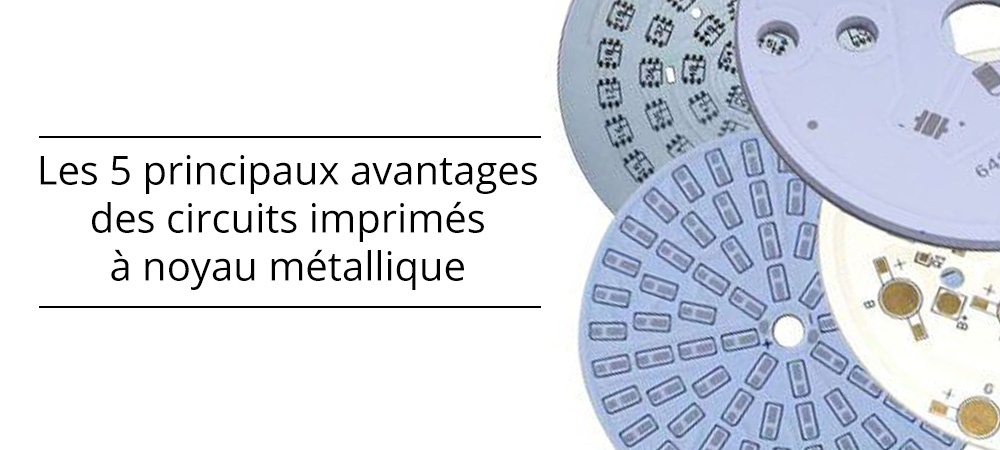
Plusieurs termes permettent de définir cette catégorie de cartes de circuits imprimés : circuit imprimé métallique, substrat métallique isolé (IMS ou IMPCB), circuit imprimé à noyau métallique (MCPCB), revêtement en aluminium, base en aluminium, etc. Bien que différentes en apparence, toutes ces définitions se rapportent au même type de circuit imprimé avec des caractéristiques techniques et des avantages identiques. Comparés aux circuits imprimés traditionnels à base de verre époxy FR-4, les circuits imprimés métalliques assurent avant tout une meilleure dissipation de la chaleur en raison d’une conductivité thermique 5 à 10 fois supérieure et d’une épaisseur jusqu’à 10 fois inférieure par rapport aux architectures conventionnelles. L’efficacité toute particulière du transfert thermique permet aux circuits imprimés métalliques d'utiliser des couches de cuivre très légères de manière à obtenir des solutions moins chères et plus minces.
Les circuits imprimés métalliques sont composés d’une couche diélectrique pouvant présenter une conductivité thermique élevée (et donc une forte dissipation de chaleur), d’une couche métallique et d’un film de cuivre ayant une capacité de dissipation thermique et une résistance mécanique élevées servant à la lithographie du circuit. L’aluminium et le cuivre sont les matériaux les plus couramment utilisés dans la fabrication de couches métalliques. L’acier inoxydable peut également être utilisé dans certaines applications. Le cuivre offre des performances et des propriétés électriques supérieures à celles de l’aluminium, mais il coûte relativement plus cher. La couche métallique peut être composée entièrement de métal, ou d’une combinaison de fibre de verre (FR-4) et de métal. Les circuits imprimés métalliques peuvent alors être à simple ou double face, tandis que la version multicouche est moins courante en raison de sa grande complexité de fabrication. Dans le cas d’un MCPCB multicouche, les différentes couches doivent être réparties uniformément par rapport à la couche métallique interne. Par exemple, dans un circuit imprimé à 12 couches, la couche métallique doit se trouver au centre de l’empilage, avec 6 couches au-dessus et 6 couches au-dessous.
Le métal étant capable de transférer facilement la chaleur issue des composants à haute puissance, on trouve parmi les applications typiques des PCB métalliques les alimentations, les convertisseurs de puissance, les systèmes d’éclairage à LED et les circuits de puissance dans les environnements automobiles (phares, feux, refroidissement, climatisation et autres). Outre une gestion thermique efficace, ce type de technologie permet de prolonger la durée de vie des composants (tels que les LED) de manière à améliorer la fiabilité de l’ensemble du circuit.
Structure et applications
La technologie MCPCB, apparue initialement dans les années 1960 pour les applications de haute puissance, est aujourd’hui largement utilisée dans les applications où il est nécessaire de maintenir une température de fonctionnement réduite. Le matériau d’isolation diélectrique, qui constitue le cœur de tout circuit imprimé métallique, est conçu pour présenter une conductivité thermique (généralement comprise entre 1 W/mK et 9 W/mK) bien supérieure à celle du FR-4 afin de garantir une évacuation efficace de la chaleur. La conductivité thermique élevée et l’épaisseur réduite de la couche isolante (cote standard de 100 µm) permettent de transférer rapidement et efficacement la chaleur produite. La conductivité thermique couramment utilisée pour la couche diélectrique est de 2 W/mK, soit une valeur bien supérieure à celle du FR-4. Plus la couche diélectrique est mince, meilleurs sont les résultats. En effet, cela permet de minimiser la distance entre les sources de chaleur et la couche métallique ayant une conductivité thermique plusieurs fois supérieure à celle du matériau diélectrique.
L’image 1 montre la structure d’un circuit imprimé métallique classique. La couche supérieure est formée d’une couche mince de cuivre sur laquelle des pistes sont gravées, à l’instar des circuits imprimés classiques. Son épaisseur est typiquement comprise entre 1 et 4 oz, mais elle peut aussi être supérieure. La couche la plus interne est constituée du matériau diélectrique qui a pour fonction d’assurer une isolation électrique entre la couche métallique et la couche de cuivre, tout en permettant un transfert thermique rapide entre les deux couches. Enfin, nous trouvons la couche métallique qui, dans la plupart des cas, est en aluminium, avec une épaisseur comprise entre 1 mm et 3,2 mm (typiquement 1,6 mm).
Image 1 : Structure typique de circuit imprimé métallique.
Parmi les principales applications des circuits imprimés métalliques, citons l’éclairage par LED, la commande des moteurs des véhicules électriques et hybrides, les relais statiques, les alimentations, les convertisseurs, les régulateurs de tension, les panneaux solaires et les cellules photovoltaïques. Plus généralement, cette technologie est adaptée aux applications qui nécessitent beaucoup d’énergie et qui, par conséquent, produisent une grande quantité de chaleur. Si le circuit imprimé doit être refroidi rapidement, il est préférable de choisir un circuit imprimé métallique plutôt qu’un substrat FR-4 traditionnel. L’aluminium, le métal le plus couramment utilisé pour la couche métallique, présente des caractéristiques électriques très avantageuses, notamment une excellente conductivité thermique, comprise entre 5 W/mK et 2 W/mK, une tension de claquage élevée (3 kV et plus) et une grande résistance à la traction.
Les 5 principaux avantages des MCPCB
Outre une excellente dissipation thermique, les circuits imprimés métalliques offrent une densité de puissance plus élevée, un blindage électromagnétique important et un couplage capacitif de meilleure qualité. Il est possible d’améliorer encore les performances thermiques en utilisant des via thermiques comme dans le cas des circuits imprimés traditionnels. Voyons maintenant les cinq principaux avantages de cette technologie.
1) Dissipation thermique
Les MCPCB font partie des circuits imprimés qui présentent une conductivité thermique élevée. L’évacuation maximale de la chaleur des composants de puissance permet d’éviter d’endommager le circuit et de gérer les circuits à haute densité et les niveaux de puissance élevés. L’aluminium est l’un des matériaux les plus répandus pour ce type de substrat. Outre ses propriétés électriques, l’aluminium présente l’avantage d’être recyclable et peu coûteux. La conductivité thermique des circuits imprimés à âme métallique est 8 à 9 fois supérieure à celle des circuits imprimés utilisant du FR-4. La couche diélectrique doit être très mince afin de minimiser la distance entre la source de chaleur et la plaque métallique de support. Son épaisseur est généralement comprise entre 75 et 150 µm. Par exemple, un test effectué sur une carte MCPCB avec une LED 1 W intégrée a montré que sa température est restée assez proche de la température ambiante de 25 °C, alors que la même LED de puissance montée sur une carte FR-4 a atteint une température dépassant de 12 °C la température ambiante.
2) Résistance et stabilité accrues
Le développement récent et rapide de la technologie LED, notamment avec l’éclairage LED à haute puissance, a soulevé des questions concernant la dissipation de la chaleur. Comme elles sont généralement montées directement sur le circuit imprimé, ces LED peuvent entraîner des problèmes de stabilité et de fiabilité du circuit. Si l’on ne recourt pas à la bonne technique, la chaleur dissipée risque de nuire aux performances des appareils électroniques fonctionnant à haute puissance. L’utilisation de circuits imprimés métalliques dans ces applications résout ce problème de manière efficace. En plus de garantir une grande résistance, l’aluminium est très léger et confère au circuit imprimé une robustesse et une résilience accrues sans entraîner d’augmentation de poids.
3) Stabilité dimensionnelle
Les dimensions d’un circuit imprimé métallique sont plus stables en fonction des conditions ambiantes que celles d’un circuit imprimé fabriqué avec des matériaux traditionnels, comme le FR-4. Soumis à une rampe de chauffage de 30 °C à environ 150 °C, les circuits imprimés comportant des couches métalliques (telles que l’aluminium) présentent de très faibles variations dans leurs dimensions : de 2,5 % à 3,0 %.
et recevez un devis pour votre projet de PCBA dans les 10 prochaines minutes !
4) Poids réduit et recyclabilité accrue
Les circuits imprimés à substrat métallique sont plus légers, durent plus longtemps et sont plus conducteurs que les circuits imprimés traditionnels fabriqués à partir de matériaux époxy. En outre, ils sont plus écologiques, car les métaux utilisés ne sont pas toxiques et se recyclent facilement, notamment l’aluminium. L’aluminium est très facile à extraire et à affiner, ce qui le rend considérablement moins cher que d’autres métaux. Par conséquent, il est également possible de réduire les coûts de fabrication liés aux circuits imprimés utilisant des substrats en aluminium. Les circuits imprimés en aluminium constituent également une solution de rechange rentable aux dissipateurs thermiques plus coûteux et plus volumineux. Il est à noter également que l’aluminium est un métal non toxique et entièrement recyclable. Tout au long de la chaîne qui relie le producteur au consommateur final, l’utilisation de l’aluminium dans les circuits imprimés métalliques contribue à la préservation de notre planète.
5) Durée de vie accrue
L’aluminium présente une robustesse et une durabilité supérieures à celles des matériaux couramment utilisés dans la fabrication des circuits imprimés, tels que la céramique et la fibre de verre. Il s’agit d’un métal très robuste qui permet de réduire les risques de rupture accidentelle pouvant survenir lors des différentes étapes de la production, de l’assemblage ou de l’utilisation normale du produit final. L’image 2 montre quelques exemples de circuits imprimés en aluminium pour des applications dans le domaine de l’éclairage LED.
Image 2 : Quelques exemples de circuits imprimés à base d’aluminium.