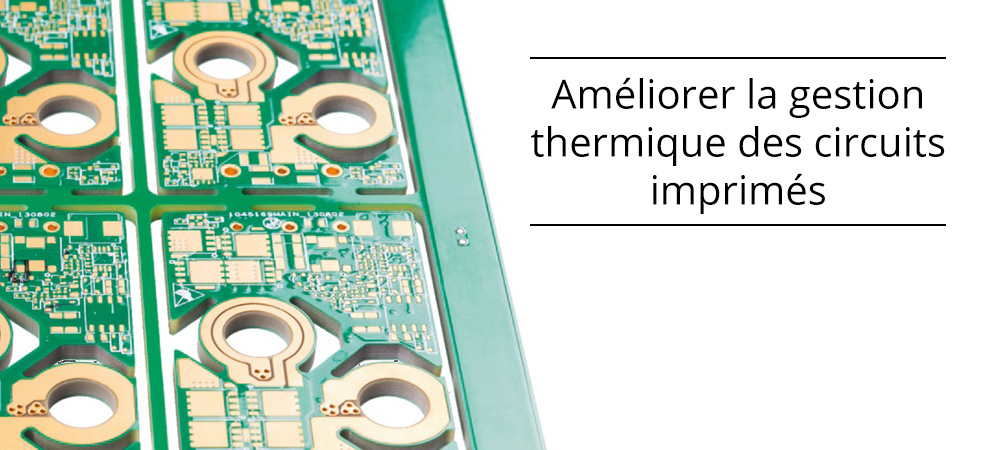
Les circuits imprimés se trouvent au cœur des appareils électroniques. Ils sont conçus pour assurer la conduction électrique et la transmission des signaux analogiques et numériques entre les différents composants électroniques. Lors de son passage dans le circuit imprimé, l’électricité génère une quantité de chaleur plus ou moins importante en fonction de la résistance qu’elle rencontre. Outre les pistes, les composants de puissance, tels que les MOSFET, les IGBT, les convertisseurs et les pilotes, sont les principaux responsables du dégagement de chaleur. Bien que les tensions d’alimentation des dispositifs logiques hautement intégrés, tels que les DSP, les SoC et les FPGA, diminuent progressivement, ceux-ci dégagent également une quantité de chaleur non négligeable en raison de leurs fréquences de fonctionnement élevées et de l’utilisation intensive d’algorithmes très complexes. La gestion thermique est l’une des problématiques les plus critiques et les plus délicates que les concepteurs de circuits imprimés doivent traiter. D’une part, il est nécessaire d’assurer le bon fonctionnement et la fiabilité du circuit à tous les niveaux de tension, de courant et de fréquence admissible ; d’autre part, il est nécessaire de respecter les contraintes budgétaires imposées par le fabricant, en limitant l’utilisation de solutions de refroidissement lourdes et coûteuses telles que les dissipateurs de chaleur, les ventilateurs ou le refroidissement par liquide.
Importance de la gestion thermique
La température de jonction des composants actuels à base de silicium est comprise entre 125 °C et 200 °C environ. Toutefois, il convient d’éviter d’atteindre cette valeur afin de ne pas détériorer rapidement la durée de vie résiduelle du composant. En fait, on estime qu’une augmentation de la température de fonctionnement de 20 °C, en raison d’une gestion thermique inefficace, est susceptible de réduire la durée de vie des composants jusqu’à 50 %. Par exemple, les LED à haute luminosité convertissent plus de 60 % de la puissance absorbée en chaleur et nécessitent donc des circuits imprimés spéciaux capables de supporter des températures élevées sans risque de détérioration des composants. La généralisation des semi-conducteurs à large bande interdite (WBG), tels que l’arséniure de gallium (GaN) et le carbure de silicium (SiC), a permis aux composants d’atteindre des températures de fonctionnement plus élevées que la technologie à base de silicium. Toutefois, il demeure nécessaire de mettre en place une gestion thermique rigoureuse en mesure de répartir uniformément la chaleur dégagée, d’éviter la formation de points d’accumulation de chaleur dangereux (points chauds) et de réduire le plus possible les pertes de puissance. L’image 1 présente un circuit électronique faisant l’objet d’un balayage thermique par une caméra infrarouge : les parties colorées en rouge correspondent aux points de plus forte concentration de chaleur.
Image 1 : Imagerie thermique du circuit imprimé.
Conseils pour assurer une gestion thermique adéquate
La première étape pour garantir une gestion thermique satisfaisante, y compris en présence de charges de forte puissance, consiste à déterminer la température de jonction TJ et la résistance thermique RT des semi-conducteurs à partir des caractéristiques techniques de chaque composant. La première grandeur peut être déduite de la fiche technique du composant, tandis que la seconde se définit comme le gradient de température le long du trajet thermique. En particulier, il est possible de réduire RT en diminuant la longueur du trajet thermique ou en augmentant la conductivité thermique du matériau et la surface des points de contact sur le circuit imprimé. Ces deux facteurs dépendent de la disposition du circuit imprimé, lequel doit donc être conçu dès le départ de manière à respecter ces exigences. La course à la miniaturisation des circuits de puissance impose des limites considérables à l’augmentation de la surface des points de contact. Ainsi, pour améliorer la gestion thermique, les concepteurs peuvent agir sur les deux facteurs suivants :
- la longueur du trajet thermique sur le circuit imprimé doit être la plus petite possible ;
- les matériaux et les substrats du circuit imprimé, ainsi que les éventuels dissipateurs de chaleur, doivent présenter la conductivité thermique la plus élevée possible.
Il est possible de répondre à la première exigence en prenant des précautions particulières lors de la conception du circuit imprimé, tandis que la seconde exige de procéder à un choix minutieux des matériaux lors des premières étapes du projet, par exemple dans le cadre de l’étude de faisabilité.
et recevez un devis pour votre projet de PCBA dans les 10 prochaines minutes !
Disposition du circuit imprimé
Les concepteurs électroniques disposent de techniques différentes pour réduire la longueur du trajet thermique sur le circuit imprimé. En premier lieu, il est conseillé d’augmenter la distance entre les pistes afin d’obtenir une répartition plus uniforme de la chaleur sur la couche et d’ainsi réduire le risque de créer des points chauds. Toutefois, cette solution est souvent limitée par la nécessité de miniaturiser la taille des circuits imprimés, comme dans le cas des produits portables. Outre la distance, la géométrie des pistes constitue un facteur essentiel. Les pistes reliant les composants de puissance doivent être les plus courtes et les plus larges possible, avec du cuivre en couche épaisse pour les pistes parcourues par des courants élevés. Pour connaître les valeurs minimales recommandées pour la largeur d’une piste en fonction de l’intensité du courant qui la traverse, il suffit de consulter les tableaux figurant dans la norme IPC-2221 relative à la conception des circuits imprimés. En cas de sous-dimensionnement des pistes pour un courant donné, il existe un risque de dégradation des performances, voire de destruction de certains composants électroniques. En cas de doute, il est toujours préférable de surdimensionner la largeur des pistes. L’insertion de via thermiques le long du chemin thermique constitue une autre technique couramment utilisée. Les via thermiques peuvent être métallisés ou non et relient plusieurs couches de manière à permettre la circulation de l’air frais et l’évacuation de la chaleur. Les via thermiques métallisées sont plus efficaces, car le revêtement de cuivre permet d’accumuler une plus grande quantité de chaleur. Outre les via thermiques, une autre technique permettant d’extraire la chaleur des composants consiste à créer de grands plans de cuivre dans le circuit imprimé afin d’augmenter la surface utile de dispersion de la chaleur. Bien que la dissipation optimale soit obtenue avec des plans en cuivre réalisés sur les couches supérieure et inférieure du circuit imprimé, où la quantité de chaleur échangée avec le milieu environnant est la plus importante, il est également possible de créer de tels plans sur les couches internes du circuit imprimé. Dans les applications de puissance, un moyen de dissiper efficacement la chaleur consiste à recourir à la technologie du cuivre lourd qui permet d’augmenter la résistance maximale du circuit imprimé au courant et à la température sans provoquer de défaillances ni de dégradation. Alors que les circuits imprimés standard présentent une épaisseur de piste d’environ 105 µm, la technologie du cuivre lourd utilise des pistes dont l’épaisseur peut atteindre 2,1 mm afin de résister à des courants de plusieurs ampères. L’image 2 montre un exemple de circuit imprimé fabriqué avec la technologie du cuivre lourd.
Image 2 : Circuit imprimé en cuivre lourd.
Choix des matériaux
Bien que le FR-4 (ignifuge niveau 4) puisse satisfaire les exigences en matière de dissipation de chaleur pour de nombreux types de circuits électroniques, plusieurs applications nécessitent des matériaux et des substrats spécifiques. Parmi ces applications figurent les circuits comportant des signaux de haute fréquence et/ou de puissance, les applications de radiofréquence (RF) et les dispositifs pour lesquels, en raison de leur compacité très élevée, il est impossible de placer des dissipateurs thermiques ou d’autres systèmes de refroidissement (électromédicaux et produits portables, principalement). Pour obtenir une bonne dissipation thermique, la constante diélectrique (Dk) du matériau doit être élevée. Bien qu’ils coûtent plus cher, les laminés Rogers répondent à cette exigence grâce à un Dk compris entre 6,15 et 11 environ, contre un Dk d’environ 4,5 pour le FR-4. De plus, ce matériau offre une grande stabilité avec la température et la fréquence, ce qui réduit les pertes de puissance, quelles que soient les conditions de fonctionnement. Une autre technique de fabrication, appelée MCPCB (Metal Core Printed Circuit Board), consiste à associer des substrats de matériaux ayant des conductivités thermiques différentes à des plans métalliques, généralement en cuivre. La technologie MCPCB emploie un préimprégné thermoconducteur placé entre les couches du circuit imprimé dont la fonction est d’extraire la chaleur des composants et de l’acheminer vers les plans métalliques. Cette technique peut utiliser un plan métallique simple ou double (les couches supérieure et inférieure du circuit imprimé). On la retrouve couramment dans les applications d’éclairage comportant des LED de puissance ou de haute luminosité. Si la chaleur produite se concentre dans un petit nombre de composants, il est également possible de recourir à la méthode de l’insert en cuivre. Le cuivre ayant une conductivité thermique élevée, des morceaux de ce métal sont insérés à l’intérieur ou à la surface du circuit imprimé, généralement sous les composants de haute puissance.
Conclusion
Pour garantir une gestion thermique efficace, il convient en premier lieu d’assurer une conception adéquate des circuits imprimés. Les concepteurs disposent désormais d’une grande variété de techniques permettant de réduire la quantité de chaleur produite et d’en améliorer la dissipation. Les principales étapes à accomplir pour parvenir à des résultats satisfaisants sont les suivantes : le choix des matériaux, les techniques de fabrication et la topologie du PCB. Les outils logiciels capables d’effectuer une analyse thermique CFD (Computational Fluid Dynamics), y compris en 3D, permettent aux concepteurs de simuler les échanges de chaleur dans l'ensemble du circuit de manière à les aider à trouver la solution la plus adaptée à l'application concernée.